Email: [email protected] Whatsapp: 8618266768780
Verlängern Sie die Lebensdauer von Baggerteilen: Tipps für Löffel und Zähne
Einführung
Bagger sind unverzichtbare Maschinen auf Baustellen, in Bergwerken und anderen Erdbewegungsprojekten. Der Löffel und die Zähne eines Baggers unterliegen während des Grab- und Ladevorgangs einem ständigen Verschleiß. Der häufige Austausch dieser Baggerteile kann teuer und zeitaufwändig werden.
Implementing good practices to extend the life of buckets, teeth, and other excavator components should be a priority for equipment owners and operators. This article will provide tips on how to prolong the lifespan of these important excavator parts.
Inspect and Maintain Buckets
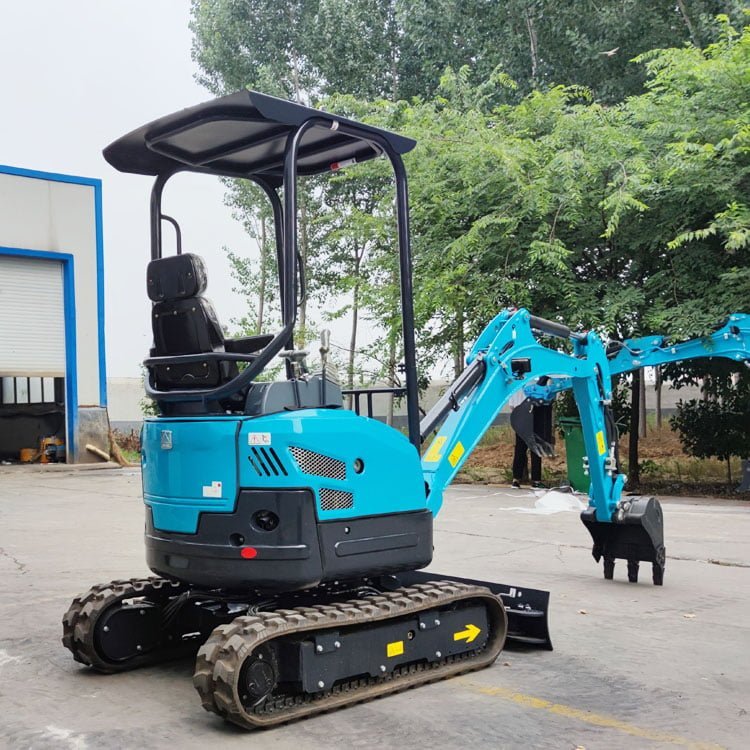
The bucket takes the brunt of the workload on an excavator. Inspecting it regularly and performing proper maintenance is key to extending its usable life.
- Inspect for cracks or holes – Catch problems early before they require major repairs. Pay special attention to high stress areas like the spill guard, side cutters, and bottom wear plates.
- Ensure fasteners are tight – Loose pins, bolts, and retainer bars lead to unnecessary wear and part replacement. Tighten them to specified torque values.
- Apply wear-resistant coatings – After replacing worn bottom and side wear plates on the bucket, have wear-resistant material welded or sprayed on. This protects the base steel underneath.
- Use the right bucket for the material – Matching bucket type to the application reduces fatigue failures. Excavator buckets come in different designs – ditching, trenching, grading, rock, heavy duty, etc.
Tooth Systems and Maintenance
Teeth on the front edge of an excavator bucket bear the impact from digging hard materials like dirt, clay, or rock. Proper tooth selection, inspection, and upkeep lead to longer life.
Tooth Styles
- Conical – General purpose earthmoving and medium impact applications
- Penetrating – High breakout force for dense material
- Abrasion resistant – For high wear applications like sand, gravel, and recycled concrete
- Heavy duty – Reinforced for extreme impact and wear resistance
Tooth Tips
- Inspect and rotate daily – Spread wear evenly and catch problems early
- Replace when worn to 50% – Don’t wait until they are completely worn
- Use proper insertion hardware – Wrong size bolts lead to cracking and looseness
- Consider regional demolition teeth – More cost effective for extreme applications
Table 1. Standard Tooth Hardware Sizes
Tooth Type | Bolt Diameter |
---|---|
Conical | 1″- 1 1/4″ |
Penetrating | 1 1/4″ – 1 1/2″ |
Heavy Duty | 1 1/2″ – 2″ |
Protect the Stick and Arm
-1.png)
The boom arms and sticks on excavators also suffer from constant stress. Follow these practices to avoid fatigue failures.
- Avoid overloading – Stay within equipment weight ratings to prevent overstressing structures
- Lubricate and inspect joints – Ensure full range of motion and catch wear early
- Use correct procedures – Improper digging techniques lead to undue structural strain
- Consider guards – Special abrasion resistant guards for sticks and arms prolong life
Part | Target Life |
---|---|
Eimer | 8,000 – 10,000 hours |
Teeth | 200 – 300 hours |
Stock | 15,000 – 20,000 hours |
Boom | 15,000 – 20,000 hours |
Conclusion:Excavator Part
Following comprehensive inspection and maintenance programs for excavator buckets, teeth, booms, sticks, and other components is essential to minimize replacement costs and downtime. While wear is inevitable in earthmoving applications, implementing these best practices will extend the usable life of these excavator parts considerably. Talk to equipment specialists about options like custom wear solutions tailored to your particular needs.
FAQ
What are the first signs that bucket teeth need to be replaced?
Look for cracks, chunks missing from the working end, or wear exceeding 50% of the tooth height. If the excavator is vibrating excessively during digging, teeth likely need replacement.
What is the recommended procedure to change Bagger teeth?
Always replace teeth in pairs on both sides of the bucket for even wear. Use proper bolt sizes and tighten bolts to the correct torque. Lastly, perform a test dig to ensure proper penetration and breakout force before resuming work.
Should I select excavator parts based on OEM brand or will aftermarket parts suffice?
For buckets and major components like booms and sticks, stick with OEM parts to ensure proper structural integrity and compatibility with the excavator. For wear parts like teeth, qualified aftermarket alternatives can provide good functionality at a lower upfront cost.
What type of welding rod should be used when re-building a worn excavator bucket?
An AWS E7018 electrode or equivalent is generally recommended for routine excavator bucket repairs and edge rebuilding. Make sure the welder has experience with excavator components. Proper preheating procedures must be followed depending on steel thickness.
Über uns
Shandong Qilu Industrial Co., Ltd. ist ein professioneller Hersteller und Exporteur, der die Entwicklung und Produktion von Baggern, Ladern und Traktoren integriert. Wir bieten absolut den besten Service.
kürzliche Posts
Video-Demo
-1.png)
Kontaktiere uns heute!
Haben Sie eine Frage, ein Angebot oder eine Anfrage? Klicken Sie auf die Schaltfläche, um eine Nachricht zu senden.
Qilu Industrial ist immer für Sie da.