Мини-экскаватор грузоподъемностью 3,5 тонны станет универсальным и мощным инструментом для выполнения различных задач по строительству, ландшафтному дизайну и сносу зданий. Эти компактные машины обеспечивают исключительную эффективность и маневренность в ограниченном пространстве, где не могут работать более крупные экскаваторы. В этом блоге мы рассмотрим, как оптимизировать использование вашего 3,5-тонного мини-экскаватора, гарантируя, что вы получите максимальную производительность и производительность от своих инвестиций.
Введение
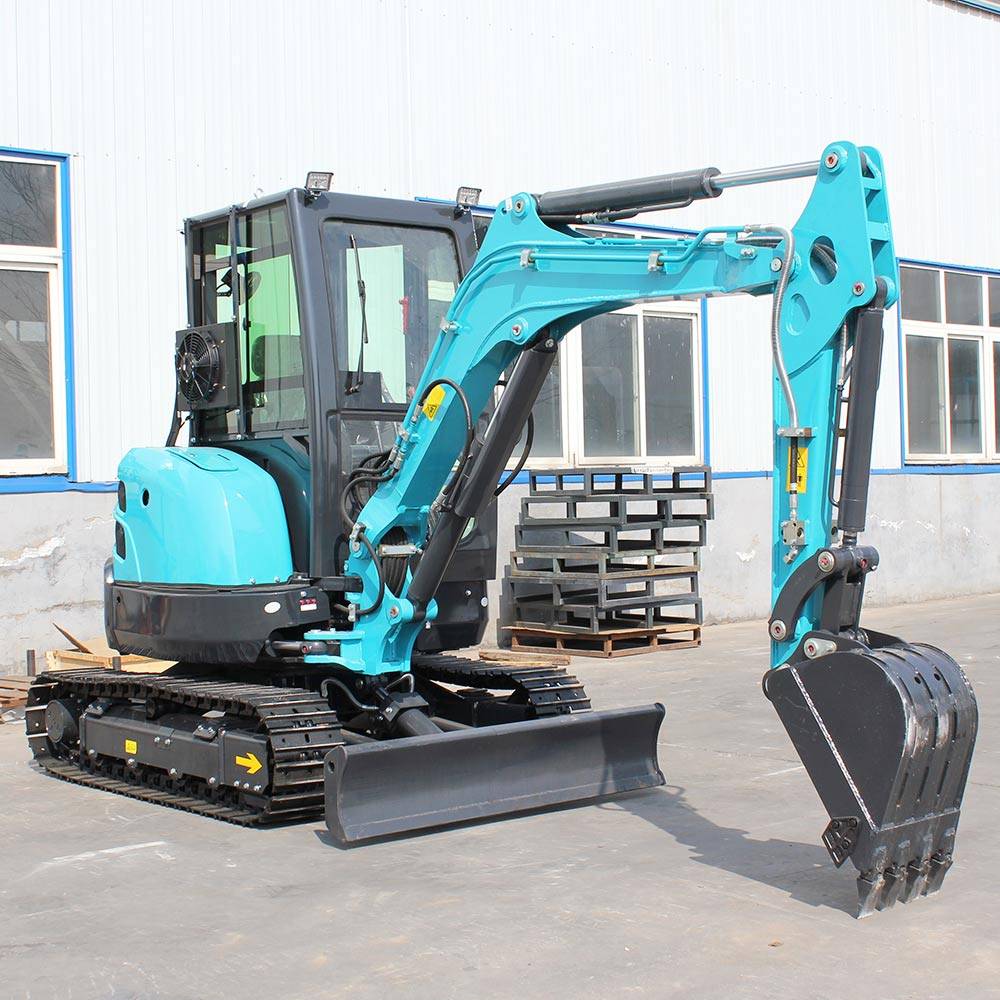
A 3.5 ton mini excavator, due to its compact size and versatility, is an invaluable asset on many job sites. It’s essential, however, to understand how to operate these machines efficiently to maximize their potential. This section will cover the basics of what makes the 3.5 ton mini excavator a popular choice for professionals in various industries.
Understanding Your 3.5 Ton Mini Excavator
To maximize the productivity of your 3.5 ton mini excavator, a deep understanding of its capabilities, limitations, and best practices for operation is essential. This segment dives into the details of operational limits, maintenance routines, and the variety of attachments available, offering insights that can enhance your efficiency and effectiveness on the job.
Operational Limits
Every mini excavator model has specific operational limits, which include maximum digging depth, reach, and loading capacity. For a 3.5 ton mini excavator, these specifications are designed to offer a balance between power and maneuverability, making them ideal for medium-scale jobs that require precision:
- Глубина и вылет копания: Typically, a 3.5 ton mini excavator can dig up to 10-15 feet deep. The arm’s reach is also crucial, allowing for efficient digging and material placement far from the machine’s base.
- Weight Capacity: The lifting capacity generally ranges from 500 to 1,000 pounds, depending on the arm’s extension and the balance of the machine. Understanding these limits is crucial to prevent overloading and potential tipping.
Maintenance Routines
Proper maintenance ensures that your 3.5 ton mini excavator operates reliably and efficiently. A well-maintained machine also has a longer lifespan and better resale value:
- Daily Checks: Conduct inspections before starting work each day. Check for any signs of wear or damage to hydraulic lines, buckets, and other attachments. Ensure that all fluids, such as hydraulic oil, engine oil, and coolant, are at the proper levels and that filters are clean.
- Regular Servicing: Follow the manufacturer’s guidelines for servicing, which typically include engine checks, hydraulic system adjustments, and the replacement of filters and oils. Regular maintenance not only prevents breakdowns but also ensures optimal performance and fuel efficiency.
Варианты вложений
The versatility of a 3.5 ton mini excavator can be significantly enhanced with the right attachments. These tools make the excavator suitable for a range of tasks from digging and grading to breaking hard materials and lifting:
- Ведра: A selection of buckets can be crucial for various tasks. A trenching bucket is narrow to dig deep, narrow excavations, while a grading bucket is wider and used for slope creation and landscaping.
- Hydraulic Hammers and Breakers: These are used for demolishing concrete and asphalt, making them indispensable for renovation and demolition projects.
- Шнеки: Enable efficient drilling into the earth, perfect for setting posts or planting trees.
- Compactors: Ideal for compacting soil in trenches or around foundations to enhance soil stability.
Операционная эффективность
Maximizing productivity starts with operating the mini excavator efficiently. Here are some tips:
- Pre-operation Checklist: Always perform a thorough check of the hydraulic systems, engine oil, and attachments.
- Efficient Techniques: Use the right technique for digging, grading, and loading to minimize fuel consumption and wear.
Strategic Use of Attachments
Attachments greatly enhance the functionality and versatility of your 3.5 ton mini excavator, turning it into a multipurpose tool that can efficiently tackle a variety of tasks across different job sites. This section delves deeper into the strategic use of various attachments, helping you optimize your mini excavator’s utility for increased productivity and flexibility.
Key Attachments and Their Strategic Uses
Selecting the right attachment for the task at hand is essential for maximizing efficiency. Here are some of the most common and effective attachments available for a 3.5 ton mini excavator, along with strategic advice on their uses:
- Гидравлические молоты: These are powerful tools for breaking up concrete, asphalt, and other hard materials. When employing a hydraulic breaker, it’s important to adjust the power settings according to the material hardness to avoid excessive wear or damage. Strategic use involves short, sharp bursts to fracture materials efficiently without overloading the excavator’s hydraulic system.
- Шнеки: Augers are ideal for drilling precise holes for landscaping, construction foundations, or fence post installations. To maximize productivity, choose an auger size that matches the hole specifications exactly and use a steady drilling speed to maintain control and avoid straining the excavator’s engine and hydraulics.
- Grapple Buckets: These attachments are excellent for sorting and moving brush, debris, and other materials. They can be particularly useful in demolition and clean-up phases of a project. The strategy here involves using the grapple to segregate materials based on size and weight, enhancing site organization and disposal efficiency.
- Compaction Wheels: Compaction wheels are used to compact soil in trenches, at the bottom of foundations, or around pilings. They provide a more accessible and cost-effective solution compared to traditional rollers, especially in confined spaces. Strategically, compaction wheels should be used in dry conditions to achieve optimal soil compaction rates.
Enhancing Efficiency with Quick Couplers
To switch between attachments quickly and safely, consider investing in quick couplers. These devices allow operators to change attachments without leaving the cab, significantly reducing downtime and increasing operational flexibility. By using quick couplers, you can swiftly adapt to changing job requirements, making your mini excavator a highly productive asset on any project.
Maintenance and Care of Attachments
Maintaining your attachments is just as crucial as maintaining the excavator itself. Regularly inspect attachment points and hydraulic connections for signs of wear or damage. Keep hydraulic components clean to prevent contamination of the system, and store attachments properly when not in use to avoid environmental damage. Scheduled maintenance extends the life of the attachments and ensures they operate at peak efficiency.
Training for Optimal Attachment Use
Ensure that all operators are properly trained on each attachment’s specific operation and limitations. Proper training reduces the risk of accidents and increases efficiency on the job site. It also helps operators understand the best practices for attachment use, such as optimal angles for digging or breaking, appropriate speeds for augering, and correct placement for compaction.
Table of Attachments and Their Uses
Тип вложения | Лучшие варианты использования | Ключевые преимущества |
---|---|---|
Hydraulic Breaker | Demolition, roadwork | High power, precise breaking |
Оже | Landscaping, post hole digging | Efficient, consistent holes |
Grapple Bucket | Material handling, landscaping | Versatility in sorting tasks |
Job Site Management
Effective management of your job site is crucial for maximizing the productivity of your 3.5 ton mini excavator. Efficient job site management not only reduces operational costs and time but also enhances safety and project outcomes. Here’s how you can strategically manage your job site to leverage the capabilities of your mini excavator fully.
Planning and Layout
Proper planning and layout of the job site are fundamental for efficient operations. Here are some strategic considerations:
- Site Assessment: Before starting any project, conduct a thorough site assessment to identify potential obstacles, such as underground utilities, overhead lines, and restricted areas that could affect excavator operations.
- Optimal Positioning: Position your mini excavator and other equipment strategically to minimize movement around the site. This reduces fuel consumption and wear and tear on machinery, as well as improves the safety of site operations.
- Material Staging: Arrange materials and waste disposal areas close to the work zones but out of the way of the primary operations. This organization minimizes the time spent moving materials and allows for smoother transitions between tasks.
Scheduling and Coordination
Effective scheduling and coordination of job site activities are essential to avoid bottlenecks and ensure continuous productivity:
- Task Scheduling: Develop a detailed schedule that outlines when each task will be performed and who will be responsible. This helps in ensuring that the mini excavator and other critical equipment are available when needed without idle time.
- Crew Coordination: Regular meetings with your team can help ensure everyone understands their roles and the day’s priorities. Effective communication prevents overlaps in tasks and equipment usage, optimizing the workflow on the job site.
Протоколы безопасности
Implementing rigorous safety protocols is not just a regulatory requirement but a necessity to ensure the well-being of all personnel on site:
- Safety Training: Regularly train all operators and onsite workers on safety practices specific to the equipment being used and the nature of the job. Include emergency response procedures in the training.
- Регулярные проверки: Conduct daily inspections of the mini excavator and other equipment to ensure they are in good working condition. Also, inspect the job site to identify and mitigate any potential hazards.
Use of Technology
Integrating technology can significantly enhance job site management:
- GPS and Machine Control Systems: Use GPS tracking and machine control systems to guide excavation depths and precision. These technologies can help in reducing errors and improving the speed of operations.
- Project Management Software: Utilize project management tools to keep track of schedules, resource allocation, and progress on tasks. These tools offer real-time updates and improve coordination among team members.
Экологические соображения
Managing the environmental impact of job site operations is crucial for compliance with regulations and for protecting the ecosystem:
- Dust Control: Implement measures to control dust, such as water sprays or dust suppressants, especially in dry areas.
- Noise Reduction: Schedule noisy operations during times that minimize impact on nearby communities and adhere to local noise regulations.
Preventative Maintenance
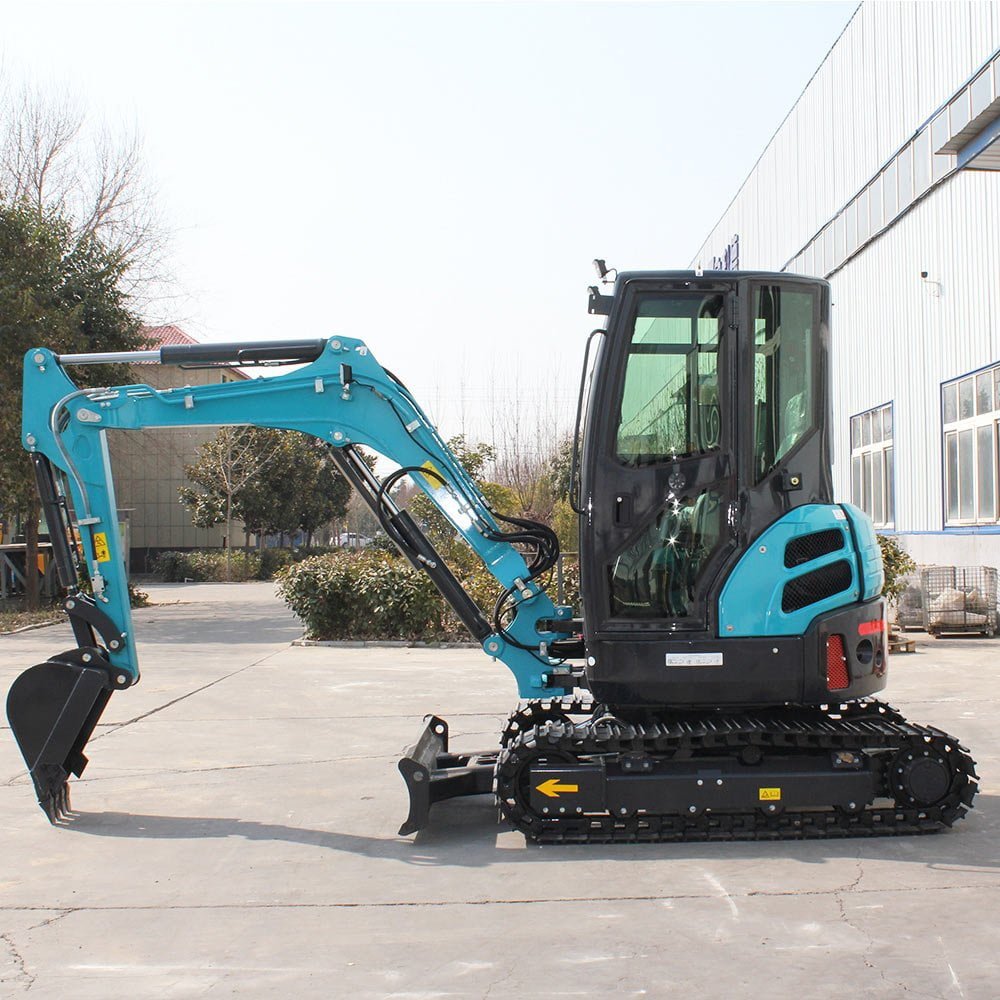
Preventative maintenance is key to extending the lifespan and maximizing the efficiency of your 3.5 ton mini excavator. This maintenance strategy not only ensures reliable machine performance but also minimizes downtime due to unexpected failures. Here are detailed guidelines on implementing an effective preventative maintenance program for your mini excavator.
Ежедневные проверки
Consistent daily inspections are the cornerstone of preventative maintenance. These checks help identify potential issues before they lead to major repairs or operational failures:
- Visual Inspection: Begin each day with a visual check of the excavator. Look for any signs of excessive wear, damage to the body, tracks or tires, and any leaks from the hydraulic system or engine.
- Fluid Levels: Check and maintain fluid levels including hydraulic oil, engine oil, and coolant. Proper fluid levels are critical for the smooth operation of the engine and hydraulic systems.
- Filters: Inspect filters regularly to ensure they are clean and free from obstructions. Dirty filters can lead to reduced performance and increased fuel consumption.
Regular Service Intervals
Adhering to the manufacturer’s recommended service intervals is crucial for maintaining your excavator in peak condition:
- Engine and Hydraulics: These systems should be serviced according to the guidelines provided by the manufacturer, typically involving oil changes, filter replacements, and hydraulic fluid refreshment.
- Undercarriage: The undercarriage should be regularly cleaned and inspected for wear and tear since it is one of the most stressed parts of the excavator. Ensure that the track tension is correct and that rollers and idlers are lubricated properly.
- Вложения: Service attachments according to their specific maintenance schedules. Regular checks will ensure that they function efficiently and last longer.
Смазка
Proper lubrication reduces friction in moving parts, decreasing wear and extending the life of the machinery:
- Greasing Joints: Regular greasing of pins and bushings is essential. Most manufacturers recommend greasing the joints every few days of operation, depending on usage intensity.
- Choice of Lubricants: Use only the lubricants recommended by the manufacturer, as these are specifically formulated to suit the operational needs of your mini excavator.
Record Keeping
Maintaining detailed records of all maintenance activities helps track the health of your equipment and can be useful for troubleshooting issues:
- Maintenance Logs: Keep a log of all maintenance and repair activities. This should include dates, details of the work performed, parts replaced, and the hours logged on the machine at the time of maintenance.
- Warranty Information: Ensure that all maintenance activities are compliant with warranty requirements. Keeping detailed records can help in making warranty claims if necessary.
Training for Maintenance
Ensure that all personnel involved in operating the excavator are trained in basic maintenance procedures:
- Operator Training: Operators should be trained not only to perform daily checks and simple maintenance tasks but also to understand signs of potential mechanical issues.
- Professional Development: Consider sending maintenance staff for further training offered by manufacturers or specialized training institutions. This keeps them updated on the latest techniques and technologies in excavator maintenance.
Вывод
A 3.5 ton mini excavator can be a powerhouse of productivity when used correctly. By understanding your machine’s capabilities, utilizing the right attachments, managing your job site efficiently, and maintaining the excavator properly, you can significantly enhance your operational efficiency and project outcomes.
Вопросы-Ответы
What should I check daily on my 3.5 ton мини-экскаватор?
Daily checks should include fluid levels (hydraulic oil, engine oil, coolant), filter conditions, and a visual inspection of attachments and undercarriage for any signs of wear or damage.
How often should I service my 3.5 ton мини-экскаватор?
Follow the manufacturer’s recommended service intervals, typically found in your machine’s user manual. Generally, major services are advised after every 500 hours of operation.
Может ли 3.5 ton mini excavator be used for demolition?
Yes, with the right attachments, such as hydraulic breakers, a 3.5 ton mini excavator can be effectively used for small-scale demolition tasks.
By adhering to these guidelines and regularly learning more about your equipment, you can ensure that your 3.5 ton mini excavator remains a reliable and effective tool for your projects.