Введение
Восьмитонные экскаваторы — это машины среднего размера, которые часто встречаются на многих строительных площадках. Они обеспечивают хороший баланс мощности, эффективности и маневренности при рытье траншей, погрузке грузовиков, сносе конструкций и выполнении различных земляных работ. Однако, как и любая тяжелая техника, 8-тонные экскаваторы могут выходить из строя и со временем требовать ремонта. В этой статье представлен подробный обзор распространенных проблем, с которыми вы можете столкнуться при использовании 8-тонного экскаватора, и способы их правильного устранения.
Frequent Engine and Hydraulic Issues
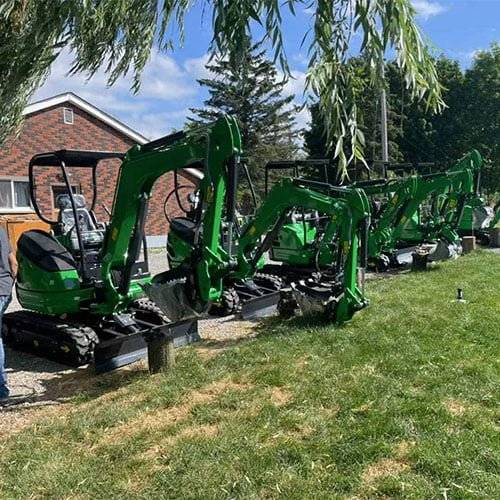
The engine and hydraulic systems are the heart of an 8 ton excavator. These complex components have many parts that wear out and can fail over years of use. Here are some of the most common engine and hydraulic faults on 8-ton excavators and their recommended repair procedures:
Overheating Engine
- Causes: Low coolant/antifreeze, faulty water pump, clogged radiator fins, failed thermostat
- Solutions: Top off coolant, test water pump operation, pressure clean radiator fins, replace thermostat
Low Engine Power
- Causes: Clogged air filter, contaminated/old fuel, faulty injectors, compression issues
- Solutions: Replace air filter, drain fuel system and refill with fresh fuel, test/replace fuel injectors, test engine compression
Hydraulic Pump Leakage
- Causes: Worn pump shaft seals, damaged pump housing
- Solutions: Replace shaft seals, rebuild or replace hydraulic pump
Slow/Jerky Boom or Arm Movement
- Causes: Low hydraulic fluid, restricted hoses, damaged control valves
- Solutions: Top off hydraulic tank, inspect hoses and fittings for blockages, test and replace damaged control valves
Table 1. Common engine and hydraulic faults and solutions
Fault | Possible Causes | Решения |
---|---|---|
Overheating Engine | Low coolant/antifreeze, faulty water pump, clogged radiator fins, failed thermostat | Top off coolant, test water pump operation, pressure clean radiator fins, replace thermostat |
Low Engine Power | Clogged air filter, contaminated/old fuel, faulty injectors, compression issues | Replace air filter, drain fuel system and refill with fresh fuel, test/replace fuel injectors, test engine compression |
Hydraulic Pump Leakage | Worn pump shaft seals, damaged pump housing | Replace shaft seals, rebuild or replace hydraulic pump |
Slow/Jerky Boom or Arm Movement | Low hydraulic fluid, restricted hoses, damaged control valves | Top off hydraulic tank, inspect hoses and fittings for blockages, test and replace damaged control valves |
Electrical Gremlins and Annoying Sensor Faults
Electrical issues and faulty sensors are common and frustrating problems on excavators. Corroded connections, damaged wires, and failed sensors can cause intermittent functionality or even leave the machine completely inoperable. Focus on the following key problems and tests when troubleshooting 8 ton excavator electrical faults:
Machine Fails to Start
- Causes: Flat or damaged battery, starter motor failure, faulty ignition switch
- Solutions: Recharge/replace battery, test starter motor amp draw, bypass ignition switch to test
Display Panel and Lights Nonfunctional
- Causes: Blown fuse, damaged wiring harness, failed switch or relay
- Solutions: Check fuses, inspect wiring for breaks and corrosion, use multimeter to test switches and relays
Sensors Give False Readings
- Causes: Loose sensor wiring, failed sensor, software calibration issue
- Solutions: Inspect sensor plugs and wires, test sensor resistance/output, recalibrate software
Table 2. Key electrical and sensor issues and troubleshooting steps
Fault | Possible Causes | Решения |
---|---|---|
Machine Fails to Start | Flat or damaged battery, starter motor failure, faulty ignition switch | Recharge/replace battery, test starter motor amp draw, bypass ignition switch to test |
Display Panel and Lights Nonfunctional | Blown fuse, damaged wiring harness, failed switch or relay | Check fuses, inspect wiring for breaks and corrosion, use multimeter to test switches and relays |
Sensors Give False Readings | Loose sensor wiring, failed sensor, software calibration issue | Inspect sensor plugs and wires, test sensor resistance/output, recalibrate software |
Common Drive Train Problems
Issues with the drivetrain that includes the tracks, final drives, rollers, idlers, and steering clutches can severely reduce mobility. Loose or severely worn parts here lead to further damage if not promptly repaired. Be attentive to these key drive system faults:
Metal-on-Metal Squeaking from Final Drives
- Causes: Low oil level, damaged gears
- Solutions: Top off final drive oil, inspect and replace damaged gears
Immobilized or Slow Track Movement
*Causes: Hydraulic failure, faulty track motor, loose/broken traction components
- Solutions: Inspect hydraulic track components, test track motor, tighten/replace broken track parts
Oil Leaking from Final Drives or Track Rollers
- Causes: Damaged seals, cracked housing, loose fittings
- Solutions: Replace seals, rebuild/replace leaky component, tighten fittings
Table 3. Common drivetrain faults and troubleshooting tips
Fault | Possible Causes | Решения |
---|---|---|
Metal-on-Metal Squeaking from Final Drives | Low oil level, damaged gears | Top off final drive oil, inspect and replace damaged gears |
Immobilized or Slow Track Movement | Hydraulic failure, faulty track motor, loose/broken traction components | Inspect hydraulic track components, test track motor, tighten/replace broken track parts |
Oil Leaking from Final Drives or Track Rollers | Damaged seals, cracked housing, loose fittings | Replace seals, rebuild/replace leaky component, tighten fittings |
Structural Damage and General Wear and Tear
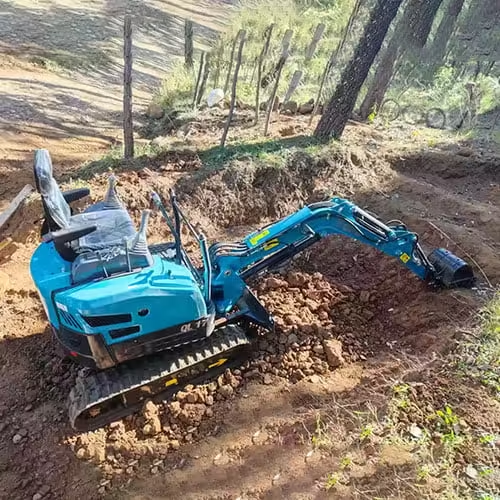
The structure of excavators takes constant abuse from contact with hard surfaces, heavy loads, and debris. Inspection and preventative repairs of cracks and damage are critical. Likewise, worn pivot bushings require rebuilding or replacement before further deflection damages fasteners, cylinders, and piping.
Cracked Boom or Arm Welds
- Causes: Fatigue cracks from repeated loading/impacts
- Solutions: Gouge and re-weld cracks, reinforce areas prone to cracks
Excessive Play in Boom and Arm Pivots
- Causes: Worn bushings
- Solutions: Measure bushing clearance and rebuild/replace worn bushings
Damaged Cab Glass with Visibility Issues
- Causes: Debris impacts from material handling operations
- Solutions: Replace cracked or damaged glass
Table 4. Structural faults and repairs
Fault | Possible Causes | Решения |
---|---|---|
Cracked Boom or Arm Welds | Fatigue cracks from repeated loading/impacts | Gouge and re-weld cracks, reinforce areas prone to cracks |
Excessive Play in Boom and Arm Pivots | Worn bushings | Measure bushing clearance and rebuild/replace worn bushings |
Damaged Cab Glass with Visibility Issues | Debris impacts from material handling operations | Replace cracked or damaged glass |
Conclusion:8 Ton Excavator
Catching problems early and performing preventative maintenance is crucial for maximizing uptime and avoiding major repairs down the road. Use the fault and repair overviews provided on engines, hydraulics, electrical systems, drivetrains, and structures as a guide when issues emerge on your 8-ton excavator. Reach out to qualified technicians if repairs are beyond your capability. Investing in routine maintenance inspections and replacing worn parts before failure will also reduce headaches by spotting issues before they snowball into bigger problems. Your excavator’s longevity and performance depend heavily on staying ahead of common faults.
Вопросы-Ответы
Q: What are the most common causes of leaks on 8-ton экскаваторы?
A: The hydraulic system is the most common source of leaks. Worn hydraulic pump seals, damaged hydraulic hoses/fittings, and leaks around hydraulic cylinders are typical causes. The engine can also leak from seals and gaskets as well as potentially the radiator and fuel lines.
Q: Why might my excavator tracks feel loose or make loud clicking noises sometimes?
A: This typically indicates worn or damaged pins, bushings, or bearings in the undercarriage components like rollers, idlers, and sprockets. Loose or broken traction parts can also cause noises and feel loose. Thorough inspection and replacement of damaged hardware is needed.
Q: What should I do if my excavator won’t swivel properly?
A: Restricted rotation is usually caused by a fault in the swing drive system. Start by checking for issues like low oil level, damaged swing gear teeth, seized bearings, or problems with the swing motor. The rotation bearing grease and bolts should also be inspected for adequate lubrication and torque.
Q: What diagnostic tools are useful when troubleshooting excavators?
A: Essential diagnostic tools include multimeters for testing electrical circuits, pressure gauges for the hydraulic systems, engine computer scanners, grease guns for lubrication analysis, infrared thermometers for identifying overheating components, and strobe lights to inspect rotating parts. Having service manuals and schematics is also critical.