Email: [email protected] Whatsapp: 8618266768780
Excavator Bucket Teeth: Materials and Durability Explained
Welcome to My Blog!
Before we dive into the content, I’d love for you to join me on my social media platforms where I share more insights, engage with the community, and post updates. Here’s how you can connect with me:
Facebook: https://www.facebook.com/profile.php?id=100072217509763
LinkedIn: https://www.linkedin.com/company/74949059/admin/dashboard/
YouTube:www.youtube.com/@tractormanufacturer-lc5qz,www.youtube.com/@excavatormanufacturers-sn9hk
TikTok: www.tiktok.com/@tractormanufacturer, www.tiktok.com/@excavatormanufacturers
Now, let’s get started on our journey together. I hope you find the content here insightful, engaging, and valuable.
Excavator bucket teeth play a vital role in the performance and efficiency of excavators, impacting digging, loading, and overall productivity on job sites. This article delves into the materials, durability factors, and considerations for choosing the right excavator bucket teeth. By understanding these elements, you can extend the lifespan of your equipment and enhance operational efficiency.
Table of Contents
- Introduction
- Why Materials Matter for Excavator Bucket Teeth
- Key Factors Influencing Durability of Excavator Bucket Teeth
- Top Materials for Excavator Bucket Teeth: A Comparison
- How to Improve the Lifespan of Excavator Bucket Teeth
- FAQ: Common Questions About Excavator Bucket Teeth
- Conclusion
Introduction
Excavator bucket teeth are essential components that directly impact the digging performance of the machine. Whether you’re working on a construction site, mining, or demolition, the right bucket teeth can make a significant difference in both productivity and cost-effectiveness. In this blog, we’ll explore the types of materials used in excavator bucket teeth and the factors that contribute to their durability. Understanding these aspects can help you choose the right bucket teeth for your specific needs, saving you time and money in the long run.
Why Materials Matter for Excavator Bucket Teeth
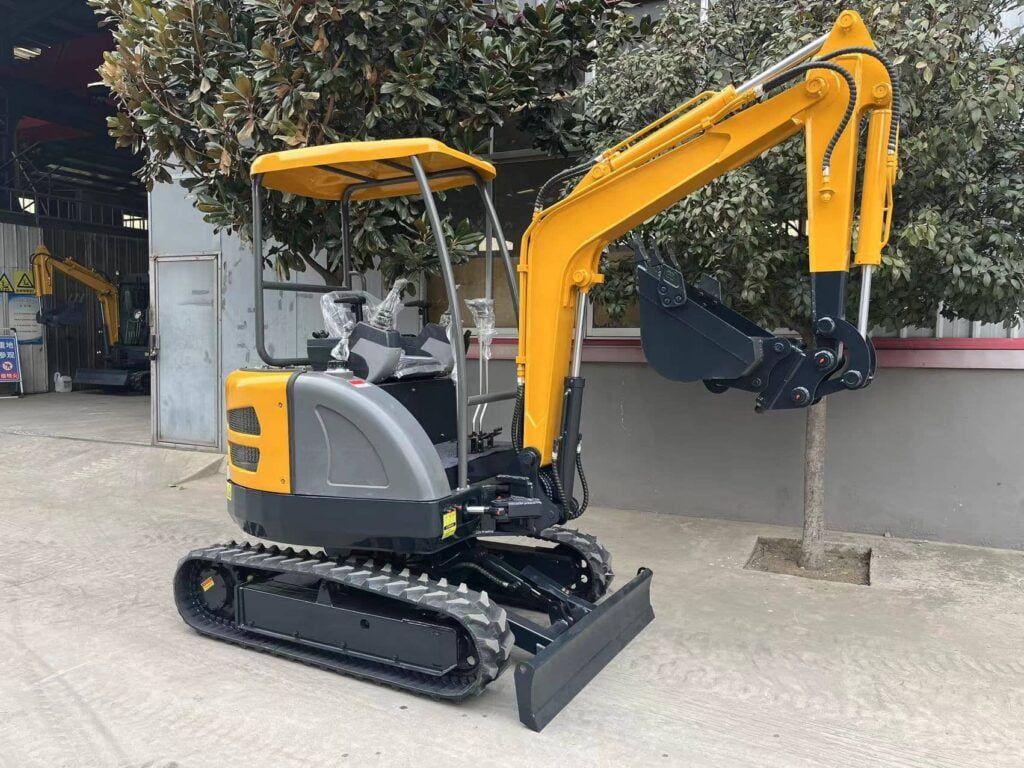
Why Materials Matter for Excavator Bucket Teeth (Expanded)
The material used in the manufacturing of excavator bucket teeth is one of the most critical factors that directly affect their overall performance, durability, and lifespan. Each material offers unique characteristics that can enhance or hinder the effectiveness of the bucket teeth depending on the nature of the job site, type of material being excavated, and specific operational demands. Here’s an in-depth look at why the choice of material matters so much when it comes to excavator bucket teeth:
1. Impact Resistance: Handling Harsh Conditions
Excavators often work in highly demanding environments where they encounter materials like hard rock, gravel, or compacted soil. The bucket teeth are repeatedly exposed to high levels of impact during these tasks, whether they are breaking through tough surfaces or scooping heavy debris. To withstand these impacts, the material used must be tough and durable. If the teeth are made from inferior materials, they can crack, chip, or wear down rapidly, leading to frequent replacements and added costs.
For instance, alloy steel is widely preferred due to its ability to handle high-impact forces without compromising on structural integrity. Its inherent toughness ensures that the bucket teeth remain intact, even during aggressive excavation.
2. Wear Resistance: Prolonging the Life of Your Equipment
Excavator bucket teeth are constantly subjected to friction and abrasion from tough materials such as rocks, sand, and gravel. Over time, this continuous wear erodes the teeth, reducing their efficiency and necessitating replacements. The material’s wear resistance plays a vital role in how long the teeth can last before needing to be replaced. The harder and more wear-resistant the material, the longer the teeth will last, leading to fewer disruptions and reduced maintenance costs.
Materials like high manganese steel, known for its high wear resistance, are often chosen for applications where the excavator will be in constant contact with abrasive materials. This material can endure the constant friction without wearing down as quickly as softer metals.
3. Hardness vs. Toughness: Finding the Right Balance
Two key properties of materials used in excavator bucket teeth are hardness and toughness, and finding the right balance between the two is essential. Hardness refers to a material’s ability to resist indentation and scratching, which is crucial when digging into hard surfaces. However, extremely hard materials may be brittle and prone to cracking or breaking under intense pressure. On the other hand, toughness refers to the material’s ability to absorb energy and resist fracturing.
A bucket tooth that is too hard may penetrate tough ground easily, but it could snap or chip if it hits a particularly hard object like a rock. Conversely, a tooth that is too tough might not break but could wear down too quickly in abrasive environments. That’s why materials like alloy steel, which strike a good balance between hardness and toughness, are commonly used in general-purpose bucket teeth.
4. Adaptability to Different Environments: Customized Solutions
The diversity of job sites and tasks demands that excavator bucket teeth be adaptable to different working conditions. For example, when working in highly abrasive environments such as sand quarries or mining operations, teeth made from tungsten carbide can offer superior wear resistance, significantly extending the lifespan of the equipment. In contrast, softer materials like carbon steel may be more suitable for light-duty operations such as trenching or excavating softer soils.
5. Cost vs. Performance: A Long-Term Investment
While high-quality materials for excavator bucket teeth often come with a higher initial cost, they can lead to significant long-term savings. Cheaper materials may wear out faster, leading to frequent replacements and increased downtime. In contrast, investing in durable, wear-resistant materials can reduce maintenance and replacement costs over time, increasing your equipment’s overall operational efficiency.
Key Factors Influencing Durability of Excavator Bucket Teeth
There are several factors that determine how long excavator bucket teeth will last. By understanding these factors, you can make informed decisions when selecting bucket teeth for your equipment.
1. Material Composition
The durability of excavator bucket teeth is heavily influenced by the composition of the materials used. High-quality alloy steel is often preferred for its excellent balance between hardness and flexibility.
2. Heat Treatment
Proper heat treatment can significantly enhance the durability of the bucket teeth. It hardens the outer surface while maintaining a tough inner core, allowing the teeth to resist wear while still being able to absorb impact.
3. Design and Fitment
Proper design and fitment of the bucket teeth are crucial for ensuring that they wear evenly and last longer. Poorly designed or ill-fitted teeth can cause uneven wear, leading to premature failure.
4. Operational Conditions
The types of materials the excavator bucket teeth encounter—whether it’s soft soil, hard rock, or abrasive gravel—can affect the rate of wear. Understanding the operational conditions is vital for choosing the appropriate material and design of bucket teeth.
5. Maintenance Practices
Regular inspection and timely replacement of worn-out teeth can prolong the life of your excavator’s bucket teeth. Neglecting maintenance can result in accelerated wear and higher costs over time.
Top Materials for Excavator Bucket Teeth: A Comparison
Selecting the best material for your excavator bucket teeth is crucial for maximizing their performance and lifespan. The table below provides a comparison of commonly used materials for excavator bucket teeth, focusing on key properties such as hardness, toughness, and wear resistance.
Material Type | Hardness (HRC) | Toughness | Wear Resistance | Best Used For |
---|---|---|---|---|
Alloy Steel (Cast) | 50-55 | High | High | General digging, sand, gravel |
High Manganese Steel | 35-40 | Very High | Moderate | Rock excavation, mining |
Chromium Steel | 60-65 | Low | Very High | Hard and abrasive materials |
Carbon Steel | 30-40 | Moderate | Low | Light-duty applications |
Tungsten Carbide-Tipped | 70+ | Low | Extremely High | Heavy-duty rock or demolition work |
As seen in the table, materials such as alloy steel and high manganese steel provide a balanced combination of toughness and wear resistance, making them suitable for most construction applications. On the other hand, tungsten carbide-tipped teeth offer the highest wear resistance, ideal for highly abrasive environments.
How to Improve the Lifespan of Excavator Bucket Teeth

While material selection plays a significant role in durability, proper usage and maintenance are equally important for extending the life of excavator bucket teeth. Here are some practical tips to improve their lifespan:
1. Routine Inspection
Frequent visual inspections can help identify wear patterns or cracks early on. This allows for timely replacement before the wear accelerates, preventing damage to the bucket.
2. Rotating Teeth
To ensure even wear, rotate the bucket teeth regularly. This practice distributes the wear across all teeth, preventing premature failure of individual teeth.
3. Using the Right Teeth for the Job
Different bucket teeth designs are optimized for different types of materials. For example, rock teeth are better suited for hard, rocky environments, while general-purpose teeth work well for softer soils. Using the correct type of teeth for your application can prevent unnecessary wear.
4. Lubrication
Applying grease or lubricants to the bucket teeth can reduce friction and abrasion, further extending their lifespan.
5. Proper Attachment
Ensure the bucket teeth are securely fastened to the bucket shank. Loose teeth can cause uneven wear or even fall off during operation, leading to downtime.
Conclusion
Excavator bucket teeth are a critical component that directly affects the performance and longevity of your machine. By selecting the right material and ensuring proper maintenance, you can maximize both the efficiency and lifespan of the bucket teeth. Alloy steel, high manganese steel, and tungsten carbide are among the top materials for durability, each suited to different operational conditions. Regular inspections, maintenance practices, and using the correct teeth for the job can further enhance their longevity, helping you get the most out of your equipment.
FAQ: Common Questions About Excavator Bucket Teeth
1. What materials are best for excavator bucket teeth?
Alloy steel and high manganese steel are commonly used for their balance between hardness and toughness. Tungsten carbide-tipped teeth are ideal for highly abrasive applications.
2. How often should I replace excavator bucket teeth?
The frequency of replacement depends on the material being excavated and the quality of the teeth. Regular inspections can help you determine when replacement is necessary.
3. What’s the difference between rock teeth and general-purpose teeth?
Rock teeth are designed for hard, abrasive materials, while general-purpose teeth are suited for softer soils and less demanding applications.
4. Can I reuse worn excavator bucket teeth?
Worn teeth can sometimes be reshaped or repaired, but it’s generally more cost-effective to replace them, especially if they are heavily worn or cracked.
5. What are signs that my bucket teeth need replacement?
Common signs include uneven wear, cracks, or broken tips. A loss of digging efficiency is another indicator that the teeth may need replacing.
About Us
Shandong Qilu Industrial Co., Ltd. is a professional manufacturer and exporter integrating the development and production of excavators, loaders and tractors. We provide the best service, absolutely.
Recent Posts
Video demo
-1.png)
Contact Us Today!
Any question, quote or inquiry? Click the button to send message.
Qilu Industrial will always here to help.