Introduction
Excavator safety is paramount on any construction site. Ensuring that all safety protocols are followed can prevent accidents, save lives, and maintain productivity. In this comprehensive guide, we will delve into the best practices and guidelines for excavator safety, offering actionable tips and insights to help you maintain a safe working environment.
Understanding Excavator Safety
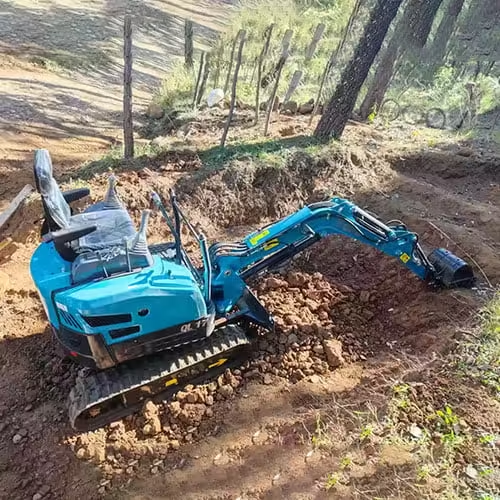
Excavator safety encompasses various aspects that are crucial to ensure a secure and efficient construction site. This includes not only the physical well-being of operators and other workers but also the operational integrity of the equipment and the organization of the work environment. Understanding the multifaceted nature of excavator safety is essential for preventing accidents, reducing downtime, and maintaining compliance with regulatory standards.
Key Components of Excavator Safety
- Operator Training: The cornerstone of excavator safety is comprehensive operator training. This training must cover the basics of machine operation, safety protocols, emergency procedures, and routine maintenance checks. Operators should be familiar with all controls and their functions, understand how to assess the site for potential hazards, and know how to respond in case of an emergency. Regular refresher courses are also crucial to keep operators updated on the latest safety practices and technological advancements.
- Equipment Maintenance: Regular maintenance and inspections of excavators are vital to ensure they are in good working condition. This involves daily checks of fluid levels, hoses, belts, and tracks, as well as scheduled maintenance according to the manufacturer’s recommendations. Keeping detailed records of all maintenance activities helps in tracking the machine’s condition and addressing any issues promptly. Proper maintenance prevents breakdowns and extends the lifespan of the equipment, contributing to overall site safety.
- Site Management: Effective site management plays a significant role in maintaining excavator safety. This includes organizing the construction site to minimize hazards, delineating specific work zones for different activities, and ensuring clear and safe pathways for both machinery and personnel. Proper site management also involves regular safety briefings and ensuring that all workers are aware of the safety protocols in place.
- Personal Protective Equipment (PPE): The use of appropriate PPE is mandatory on construction sites to protect workers from potential injuries. For those operating or working near excavators, essential PPE includes helmets, gloves, safety glasses, and high-visibility clothing. Ensuring that all workers consistently wear the necessary PPE is a fundamental aspect of excavator safety.
- Clear Communication: Effective communication is critical to maintaining safety on a construction site. Operators and ground workers should use established hand signals or radios to communicate clearly and promptly. This helps in coordinating movements, especially in tight or crowded areas, and in alerting others to any potential dangers.
Operator Training and Certification
One of the most critical components of excavator safety is ensuring that operators are well-trained and certified. Proper training programs should cover both theoretical knowledge and practical skills, making sure that operators are competent and confident in their ability to handle the equipment safely. Here’s an in-depth look at the essential aspects of operator training and certification:
Comprehensive Training Programs
Machine Operation
The foundation of any training program is a thorough understanding of machine operation. This includes familiarizing operators with the various controls, functions, and features of the excavator. They should know how to start, maneuver, and shut down the machine safely. Additionally, operators need to understand the capabilities and limitations of the excavator, including load limits and the correct use of attachments. Practical training sessions should involve hands-on practice under the supervision of experienced trainers, allowing operators to gain confidence and proficiency.
Safety Protocols
Operators must be well-versed in the safety protocols associated with excavator operation. This involves understanding how to conduct pre-operation checks, recognizing and avoiding potential hazards, and following safe work practices. Training should cover emergency procedures, such as how to safely shut down the machine in the event of a malfunction or accident. Operators should also be trained on the importance of wearing personal protective equipment (PPE) and ensuring that all safety guards and devices are in place and functional.
Site Assessment
A crucial part of operator training is learning how to assess the work site for potential hazards. Operators should be trained to identify unstable ground conditions, overhead obstacles, underground utilities, and other environmental factors that could impact the safe operation of the excavator. They should also be able to interpret site plans and understand the layout and boundaries of the work zone. Conducting a thorough site assessment before beginning operations helps in planning safe and efficient work processes.
Regulatory Compliance
Operators must be knowledgeable about the regulatory standards and guidelines governing excavator operations. This includes understanding the Occupational Safety and Health Administration (OSHA) regulations, local and state laws, and industry best practices. Training programs should incorporate these regulations, ensuring that operators are aware of their legal responsibilities and the importance of compliance. Certification programs often include a written test to assess the operator’s understanding of these regulations.
Refresher Courses
To maintain a high level of safety and proficiency, operators should undergo regular refresher courses. These courses help to reinforce existing knowledge, introduce new safety practices, and keep operators updated on any changes in regulations or technology. Refresher training is particularly important for experienced operators to prevent complacency and ensure they continue to operate excavators safely and efficiently. It is also an opportunity to address any bad habits that may have developed over time and correct them.
Certification Process
The certification process typically involves a combination of classroom instruction, hands-on training, and assessment. Upon successful completion of the training program, operators receive certification, which validates their competence and knowledge. This certification is not only a legal requirement in many regions but also a mark of professionalism and commitment to safety. Certified operators are generally more respected in the industry and have better job prospects.
Benefits of Proper Training and Certification
- Enhanced Safety: Proper training ensures that operators are equipped with the knowledge and skills needed to operate excavators safely, significantly reducing the risk of accidents and injuries.
- Increased Efficiency: Trained operators can perform their tasks more efficiently, leading to improved productivity and reduced downtime.
- Regulatory Compliance: Certification ensures that operators meet legal requirements, protecting the company from potential fines and legal issues.
- Professional Development: Training and certification contribute to the professional development of operators, enhancing their career prospects and job satisfaction.
Routine Maintenance and Inspections
Maintaining excavator safety heavily relies on the regular maintenance and inspection of the equipment. Proper maintenance ensures that the excavator operates efficiently and reduces the likelihood of unexpected breakdowns or accidents. Here’s an in-depth look at the key aspects of routine maintenance and inspections:
Importance of Regular Maintenance
Routine maintenance is crucial for keeping excavators in optimal working condition. It helps in identifying and addressing potential issues before they escalate into major problems, thereby enhancing the safety and longevity of the equipment. Regular maintenance also ensures that the excavator performs efficiently, reducing fuel consumption and operational costs.
Daily Inspections
Daily inspections are the first line of defense against equipment failure and accidents. Operators should perform a thorough check of the excavator before starting their shift. These inspections should cover several critical areas:
- Fluid Levels: Checking the levels of engine oil, hydraulic fluid, coolant, and fuel to ensure they are within the recommended ranges.
- Hoses and Belts: Inspecting hoses and belts for signs of wear, cracks, or leaks. Damaged hoses and belts should be replaced immediately to prevent failures.
- Tracks and Tires: Examining the tracks or tires for wear and tear, proper tension, and any foreign objects that could cause damage.
- Attachments: Ensuring that all attachments are securely fastened and in good working condition.
- Electrical Systems: Checking the lights, signals, and battery connections to ensure they are functioning correctly.
- Safety Devices: Verifying that safety devices such as alarms, horns, and backup cameras are operational.
Scheduled Maintenance
In addition to daily inspections, excavators require more comprehensive maintenance at regular intervals as specified by the manufacturer. Scheduled maintenance includes a detailed examination of the machine’s components and systems:
- Engine: Regularly changing the engine oil and filters to keep the engine running smoothly. Inspecting the air filter and replacing it if necessary.
- Hydraulic System: Checking hydraulic hoses, cylinders, and connections for leaks or damage. Replacing hydraulic fluid and filters as recommended.
- Undercarriage: Conducting a thorough inspection of the undercarriage, including tracks, rollers, and idlers. Cleaning and lubricating moving parts to prevent wear.
- Cooling System: Flushing and refilling the coolant system periodically to prevent overheating. Checking the radiator and coolant lines for leaks or blockages.
- Electrical System: Inspecting the alternator, starter, and wiring for any signs of wear or damage. Ensuring that all electrical connections are secure.
- Boom and Arm: Examining the boom and arm for cracks, dents, or other damage. Lubricating pivot points and checking for proper movement.
Record Keeping
Maintaining detailed records of all maintenance activities is essential for tracking the condition of the excavator and planning future maintenance. These records should include:
- Inspection Reports: Documenting the findings of daily and scheduled inspections, noting any issues identified and the actions taken to address them.
- Maintenance Logs: Keeping a log of all maintenance activities, including the date, description of the work performed, and the name of the technician who performed it.
- Repair History: Recording all repairs made to the excavator, including the parts replaced and the cost of the repairs.
- Service Intervals: Tracking the hours of operation and scheduling maintenance based on the manufacturer’s recommended service intervals.
Immediate Repairs
When issues are identified during inspections or regular operations, it is crucial to address them immediately. Delaying repairs can lead to equipment failure, which not only increases repair costs but also poses significant safety risks. Operators should be trained to recognize warning signs and report any issues promptly. Having a proactive approach to repairs ensures that the excavator remains safe and reliable.
Benefits of Routine Maintenance and Inspections
- Enhanced Safety: Regular maintenance and inspections help in identifying and mitigating potential hazards, reducing the risk of accidents and injuries.
- Increased Equipment Lifespan: Keeping the excavator in good condition through regular maintenance extends its operational life and improves its resale value.
- Improved Performance: Well-maintained equipment performs more efficiently, reducing fuel consumption and operational costs.
- Reduced Downtime: Identifying and addressing issues before they cause equipment failure minimizes unplanned downtime, ensuring that projects stay on schedule.
- Regulatory Compliance: Regular maintenance and accurate record-keeping help in complying with regulatory requirements, avoiding fines and legal issues.
Maintenance Checklist Table
To ensure that all critical maintenance tasks are performed consistently, a detailed maintenance checklist should be followed. Below is an example of a comprehensive maintenance checklist for excavators:
Maintenance Task | Frequency | Description |
---|---|---|
Check fluid levels | Daily | Ensure engine oil, hydraulic fluid, coolant, and fuel are adequate. |
Inspect hoses and belts | Daily | Look for signs of wear, cracks, or leaks. |
Examine tracks/tires | Daily | Check for proper tension and any foreign objects. |
Test electrical systems | Daily | Verify lights, signals, and battery connections. |
Inspect safety devices | Daily | Ensure alarms, horns, and backup cameras are operational. |
Change engine oil and filters | As per schedule | Replace oil and filters regularly to maintain engine performance. |
Check hydraulic system | As per schedule | Inspect hoses, cylinders, and connections; replace fluid and filters. |
Inspect undercarriage | As per schedule | Clean, lubricate, and check for wear in tracks, rollers, and idlers. |
Maintain cooling system | As per schedule | Flush and refill coolant; check radiator and coolant lines. |
Inspect electrical system | As per schedule | Check alternator, starter, and wiring for wear or damage. |
Examine boom and arm | As per schedule | Look for cracks or dents; lubricate pivot points. |
Safe Operation Practices
Implementing safe operation practices is vital for minimizing risks on the construction site. Safe operation practices involve a combination of pre-operation checks, clear communication, proper loading techniques, and adherence to speed limits. By following these guidelines, operators can ensure that they handle the excavator safely, thereby protecting themselves, their coworkers, and the equipment. Here’s a detailed look at the key aspects of safe operation practices:
Pre-Operation Checks
Before starting the excavator, operators should conduct thorough pre-operation checks. These checks are essential for identifying any potential issues that could compromise safety or efficiency during operation.
Key Pre-Operation Checks:
- Fluid Levels: Verify that engine oil, hydraulic fluid, coolant, and fuel levels are adequate.
- Visual Inspection: Conduct a walk-around inspection to check for any visible damage or leaks.
- Attachments: Ensure that all attachments are securely fastened and in good working condition.
- Tires and Tracks: Inspect tires or tracks for wear and proper tension.
- Safety Devices: Test safety devices such as alarms, horns, and backup cameras to ensure they are functioning correctly.
- Controls: Check that all controls are operating smoothly and that there are no unusual noises or vibrations.
Clear Communication
Effective communication is crucial for maintaining safety on a construction site. Operators and ground workers must use clear signals and communication methods to coordinate their activities and avoid accidents.
Communication Best Practices:
- Hand Signals: Use standardized hand signals that are understood by all team members for directing operations.
- Radios: Equip operators and key personnel with radios for real-time communication, especially in noisy environments.
- Visual Cues: Use high-visibility clothing and flags to enhance visibility and communication.
- Pre-Operation Meetings: Conduct briefings before the start of each shift to discuss the day’s tasks, potential hazards, and safety protocols.
- Emergency Signals: Establish specific signals or codes to indicate emergencies or the need to stop operations immediately.
Proper Loading Techniques
Proper loading techniques are essential for maintaining stability and preventing accidents during excavator operations. Overloading or improperly balanced loads can lead to tip-overs and other hazardous situations.
Loading Safety Guidelines:
- Weight Limits: Always adhere to the manufacturer’s recommended weight limits for the excavator and its attachments.
- Load Distribution: Ensure that loads are evenly distributed to maintain the machine’s balance and stability.
- Securing Loads: Use appropriate restraints or securing methods to prevent loads from shifting during transport.
- Stable Ground: Operate the excavator on stable and level ground to prevent tipping.
- Avoiding Overhead Obstacles: Be mindful of overhead obstacles such as power lines and structures when lifting and moving loads.
Adhering to Speed Limits
Operating the excavator at safe speeds is crucial for maintaining control and preventing accidents. Speed limits should be observed not only for the machine’s movement but also for the swing speed of the boom.
Speed Management Tips:
- Controlled Movement: Move the excavator at a slow and controlled pace, especially in tight or crowded areas.
- Swing Speed: Adjust the swing speed of the boom to match the task and surrounding conditions.
- Awareness of Surroundings: Maintain constant awareness of the environment, including other workers and machinery.
- Gradual Movements: Avoid sudden or jerky movements that can cause instability or loss of control.
- Braking Distance: Allow adequate distance for stopping the excavator safely, particularly when carrying loads.
Other Safe Operation Practices
In addition to the primary aspects mentioned above, several other practices contribute to safe excavator operation:
- Operator Fatigue: Monitor operator fatigue levels and ensure that operators take regular breaks. Fatigue can significantly impair judgment and reaction times.
- Weather Conditions: Adjust operation techniques based on weather conditions. For instance, wet or icy conditions require extra caution and reduced speeds.
- Emergency Procedures: Ensure that all operators are familiar with emergency procedures and know how to quickly and safely shut down the excavator in case of an emergency.
- Buddy System: Implement a buddy system where operators work in pairs or small teams, enhancing safety through mutual oversight and assistance.
- Continuous Training: Provide ongoing training to operators to reinforce safe operation practices and keep them updated on new safety guidelines and equipment features.
Summary of Safe Operation Practices
Safety Practice | Description |
---|---|
Pre-Operation Checks | Conduct thorough inspections of the excavator before each shift. |
Clear Communication | Use hand signals, radios, and visual cues for effective communication. |
Proper Loading Techniques | Ensure loads are within weight limits and properly balanced. |
Adhering to Speed Limits | Operate at safe speeds and adjust for environmental conditions. |
Operator Fatigue Management | Monitor fatigue levels and ensure regular breaks for operators. |
Weather Condition Adjustments | Modify operation techniques based on weather conditions. |
Emergency Procedures | Familiarize operators with emergency shutdown procedures. |
Buddy System | Implement a buddy system for enhanced safety oversight. |
Continuous Training | Provide ongoing training to reinforce safe operation practices. |
Site Management and Hazard Prevention
Effective site management is crucial for ensuring excavator safety and preventing hazards on the construction site. Proper organization, clear demarcation of work zones, and proactive hazard identification can significantly reduce the risk of accidents and improve overall efficiency. Here’s a comprehensive look at the key aspects of site management and hazard prevention:
Organized Site Layout
A well-organized site layout is the foundation of safe excavator operations. This involves planning and arranging the site in a way that minimizes risks and enhances workflow.
Key Elements of an Organized Site:
- Zoning: Clearly delineate work zones, including areas for excavator operations, material storage, and pedestrian pathways. This helps in avoiding overlap between heavy machinery and foot traffic.
- Access Routes: Designate specific access routes for excavators and other vehicles to prevent congestion and ensure smooth movement. These routes should be clearly marked and free from obstructions.
- Staging Areas: Set up designated staging areas for equipment and materials. This keeps the site organized and reduces the risk of tripping hazards and collisions.
- Lighting: Ensure adequate lighting, especially in low-light conditions or during night shifts. Proper lighting helps operators see clearly and avoid accidents.
Hazard Identification and Mitigation
Regularly identifying and mitigating potential hazards is essential for maintaining a safe work environment. This involves conducting thorough site assessments and implementing measures to address identified risks.
Hazard Identification Steps:
- Site Assessments: Conduct regular site assessments to identify potential hazards such as unstable ground, overhead obstacles, and underground utilities.
- Risk Analysis: Analyze identified hazards to determine their potential impact and the likelihood of occurrence. Prioritize hazards based on their severity.
- Preventive Measures: Implement preventive measures to address hazards. This can include reinforcing unstable ground, marking underground utilities, and removing overhead obstacles.
- Monitoring: Continuously monitor the site for new hazards that may arise as work progresses. Regular assessments help in keeping the site safe and adapting to changing conditions.
Barricades and Signage
Using barricades and signage effectively can prevent unauthorized access to dangerous areas and guide workers safely around the site.
Effective Use of Barricades and Signage:
- Physical Barriers: Erect physical barriers such as fences, cones, and barricades around hazardous areas. This prevents unauthorized entry and protects workers from potential dangers.
- Warning Signs: Place clear and visible warning signs around hazardous areas to alert workers of potential risks. Signs should be easily readable and positioned at strategic locations.
- Directional Signage: Use directional signs to guide workers and machinery along safe paths. This helps in maintaining an organized flow of movement on the site.
- Safety Notices: Post safety notices at prominent locations, including emergency contact numbers, evacuation routes, and first aid stations.
Clear Pathways and Housekeeping
Maintaining clear pathways and practicing good housekeeping are vital for preventing accidents and ensuring smooth operations.
Housekeeping Practices:
- Regular Cleaning: Keep the site clean and free from debris, which can cause tripping hazards or obstruct equipment movement.
- Tool and Equipment Storage: Store tools and equipment in designated areas when not in use. This prevents clutter and reduces the risk of accidents.
- Spill Management: Address spills immediately to prevent slip and fall accidents. Use appropriate spill containment and cleanup procedures.
- Waste Disposal: Set up waste disposal bins and ensure regular removal of construction debris and waste materials.
Regular Safety Inspections
Conducting regular safety inspections is essential for identifying and addressing potential hazards before they cause accidents.
Safety Inspection Guidelines:
- Inspection Schedule: Establish a schedule for regular safety inspections, including daily walk-throughs and more comprehensive weekly or monthly inspections.
- Inspection Checklist: Use a detailed checklist to ensure all areas and potential hazards are covered during inspections. This includes equipment, work zones, and housekeeping practices.
- Reporting and Documentation: Document the findings of each inspection and report any issues to the relevant authorities. Maintain records for accountability and future reference.
- Corrective Actions: Implement corrective actions promptly to address any identified hazards. Follow up to ensure that the actions are effective and hazards are mitigated.
Training and Safety Briefings
Regular training and safety briefings are essential for keeping all workers informed about safety protocols and best practices.
Training and Briefing Practices:
- Safety Training: Provide regular safety training to all workers, including new hires and experienced personnel. Training should cover site-specific hazards, safe operation practices, and emergency procedures.
- Toolbox Talks: Conduct daily toolbox talks to discuss specific tasks, potential hazards, and safety measures for the day’s work. This keeps safety at the forefront of everyone’s mind.
- Emergency Drills: Perform regular emergency drills to ensure that all workers know how to respond in case of an emergency. Drills should cover evacuation procedures, first aid response, and communication protocols.
- Feedback and Improvement: Encourage workers to provide feedback on safety practices and report any concerns. Use this feedback to continuously improve safety measures and address any gaps.
Summary of Site Management and Hazard Prevention Practices
Practice | Description |
---|---|
Organized Site Layout | Plan and arrange the site to minimize risks and enhance workflow. |
Hazard Identification | Conduct regular site assessments and implement measures to mitigate hazards. |
Barricades and Signage | Use physical barriers and warning signs to prevent unauthorized access. |
Clear Pathways and Housekeeping | Maintain clear pathways and practice good housekeeping to prevent accidents. |
Regular Safety Inspections | Conduct scheduled safety inspections to identify and address potential hazards. |
Training and Safety Briefings | Provide regular training and briefings to keep workers informed about safety. |
Personal Protective Equipment (PPE)
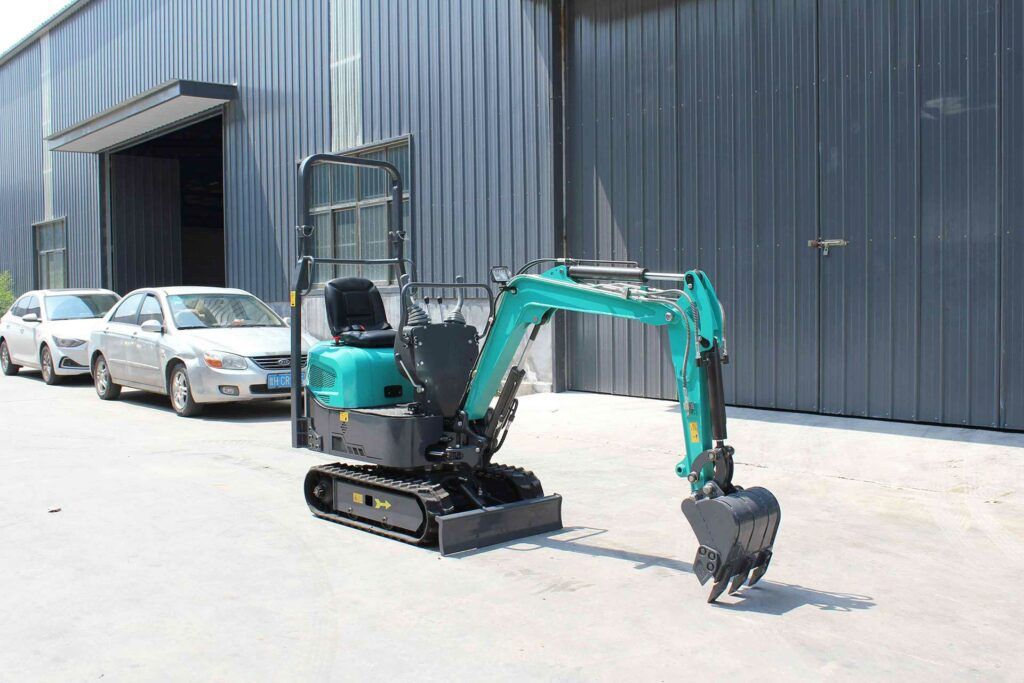
Ensuring that all workers on-site are equipped with the necessary personal protective equipment (PPE) is a fundamental aspect of excavator safety. PPE acts as the last line of defense against workplace hazards, providing protection to workers from injuries and accidents that could occur during excavator operations. Here’s an in-depth look at the various types of PPE required on construction sites and their importance:
Importance of PPE
PPE is essential for minimizing the risk of injury in hazardous work environments. It provides a barrier between the worker and potential dangers, ensuring that even if an accident occurs, the impact on the worker is minimized. Proper use of PPE not only protects the individual but also contributes to the overall safety culture of the site.
Types of PPE for Excavator Operators
1. Helmets
Helmets are crucial for protecting workers from head injuries caused by falling objects or accidental bumps. They are designed to absorb impact and prevent severe head trauma.
- Features: Helmets should have a hard outer shell, a comfortable inner lining, and a chin strap to keep them securely in place.
- Inspection and Maintenance: Regularly inspect helmets for cracks, dents, or other signs of damage. Replace any helmet that has sustained a significant impact or shows wear and tear.
2. Safety Glasses and Face Shields
Eye protection is vital to shield workers from flying debris, dust, and other particles that could cause eye injuries. Safety glasses and face shields provide a clear view while protecting the eyes and face.
- Types: Safety glasses should have impact-resistant lenses, while face shields provide additional coverage for the entire face.
- Care: Clean lenses regularly to ensure clear vision. Replace any damaged or scratched eyewear to maintain protection.
3. Hearing Protection
Excavator operations can generate high levels of noise that can cause hearing damage over time. Hearing protection devices such as earplugs or earmuffs are essential to protect workers’ hearing.
- Selection: Choose hearing protection that fits comfortably and provides adequate noise reduction.
- Usage: Ensure that earplugs are inserted correctly and earmuffs are adjusted to create a proper seal.
4. Gloves
Gloves protect workers’ hands from cuts, abrasions, and chemical exposure. They also improve grip, reducing the risk of accidents caused by slipping.
- Types: Use gloves appropriate for the task, such as heavy-duty gloves for handling materials or chemical-resistant gloves when working with hazardous substances.
- Maintenance: Inspect gloves for tears or holes and replace them as needed. Clean gloves according to the manufacturer’s instructions to maintain their protective qualities.
5. High-Visibility Clothing
High-visibility clothing ensures that workers are easily seen by machine operators and other personnel, especially in low-light conditions or busy construction sites.
- Features: High-visibility clothing should be bright and include reflective strips for visibility from all angles.
- Standards: Follow safety standards for high-visibility apparel, ensuring that clothing meets the required specifications for your work environment.
6. Safety Boots
Safety boots protect workers’ feet from heavy objects, sharp debris, and slips. They should provide both impact resistance and slip protection.
- Types: Choose boots with steel toes for impact protection and non-slip soles for traction on various surfaces.
- Fit and Comfort: Ensure that boots fit well and provide adequate support to prevent foot fatigue during long shifts.
Implementation and Enforcement of PPE Usage
Ensuring that all workers wear the appropriate PPE requires a systematic approach. It involves training, regular monitoring, and strict enforcement to maintain a high level of compliance.
Training
Provide comprehensive training on the importance of PPE, how to wear it correctly, and how to maintain it. Training should cover the specific types of PPE required for different tasks and the potential hazards each type protects against.
Monitoring
Regularly monitor the site to ensure that all workers are wearing the required PPE. Supervisors should conduct spot checks and reinforce the importance of PPE compliance. Use checklists to document compliance and identify areas for improvement.
Enforcement
Enforce PPE usage through clear policies and consequences for non-compliance. Make it clear that PPE is mandatory and that failure to wear it will result in disciplinary action. Provide replacement PPE on-site to ensure that workers always have access to the necessary equipment.
Benefits of Proper PPE Usage
- Injury Prevention: Reduces the risk of injuries from common construction hazards such as falling objects, sharp materials, and loud noises.
- Legal Compliance: Ensures compliance with occupational safety regulations, avoiding fines and legal issues.
- Enhanced Productivity: Workers who feel safe are more productive and focused, reducing downtime due to injuries.
- Safety Culture: Promotes a culture of safety where workers take responsibility for their own protection and look out for their colleagues.
Summary of PPE Requirements
PPE Type | Purpose | Key Features |
---|---|---|
Helmets | Protects head from impact and falling objects | Hard outer shell, comfortable lining, secure chin strap |
Safety Glasses/Face Shields | Shields eyes and face from debris and particles | Impact-resistant lenses, full-face coverage (for face shields) |
Hearing Protection | Protects hearing from high noise levels | Earplugs or earmuffs, adequate noise reduction |
Gloves | Protects hands from cuts, abrasions, chemicals | Task-appropriate material, good grip, tear-resistant |
High-Visibility Clothing | Ensures workers are easily seen | Bright colors, reflective strips |
Safety Boots | Protects feet from impacts and slips | Steel toes, non-slip soles, comfortable fit |
Excavator Safety Guidelines Table
Safety Measure | Description | Frequency |
---|---|---|
Operator Training | Comprehensive training program for all operators. | Initial and annual |
Daily Inspections | Routine checks of fluid levels, hoses, belts, and tracks. | Daily |
Scheduled Maintenance | Detailed inspections according to manufacturer’s recommendations. | Monthly/Quarterly |
Pre-Operation Checks | Thorough checks before starting the machine. | Daily |
Clear Communication | Use of signals or radios for effective communication. | Continuous |
Proper Loading Techniques | Ensuring balanced and safe loading of materials. | Continuous |
Site Zoning | Designating specific work zones for excavator operations. | Continuous |
PPE Enforcement | Ensuring all workers wear appropriate safety gear. | Continuous |
Regular Site Assessments | Frequent inspections to identify and mitigate potential hazards. | Weekly/As needed |
Emergency Preparedness
Being prepared for emergencies is a critical component of excavator safety. Emergency preparedness involves having a well-developed response plan, ensuring that all workers are familiar with it, and conducting regular drills to maintain readiness. Proper preparation can significantly reduce the impact of emergencies and protect the lives and well-being of workers on-site. Here’s an in-depth look at the key aspects of emergency preparedness:
Developing an Emergency Response Plan
An effective emergency response plan outlines the procedures to follow in various emergency situations. This plan should be tailored to the specific risks and conditions of the construction site and must be easily accessible to all workers.
Key Elements of an Emergency Response Plan:
- Identification of Potential Emergencies: Identify the types of emergencies that could occur on the construction site, such as fires, equipment malfunctions, medical emergencies, chemical spills, and natural disasters.
- Roles and Responsibilities: Clearly define the roles and responsibilities of each worker during an emergency. This includes identifying who will call emergency services, who will lead evacuations, and who will administer first aid.
- Emergency Contacts: Maintain a list of emergency contacts, including local emergency services, company safety officers, and nearby medical facilities. This list should be prominently displayed and easily accessible.
- Evacuation Routes and Assembly Points: Designate primary and secondary evacuation routes and establish safe assembly points where workers should gather after evacuating. These routes and points should be clearly marked and communicated to all workers.
- Communication Plan: Establish a communication plan that includes methods for alerting workers to an emergency, such as alarms, sirens, or radio announcements. Ensure that there are procedures for maintaining communication during and after the emergency.
- Emergency Equipment: Identify the locations of emergency equipment such as fire extinguishers, first aid kits, eye wash stations, and spill containment kits. Ensure that these are regularly inspected and maintained.
Training and Familiarization
Training workers on the emergency response plan is essential for ensuring that everyone knows what to do in case of an emergency. This training should be conducted regularly and include both new hires and existing employees.
Training Components:
- Plan Overview: Provide an overview of the emergency response plan, explaining the potential emergencies, roles and responsibilities, and procedures.
- Evacuation Drills: Conduct regular evacuation drills to practice the routes and procedures. These drills should simulate different emergency scenarios to ensure that workers are prepared for various situations.
- First Aid Training: Offer first aid training to a designated group of workers. This training should cover basic first aid techniques, CPR, and the use of automated external defibrillators (AEDs).
- Equipment Use: Train workers on the proper use of emergency equipment such as fire extinguishers and spill containment kits. Ensure that they know where this equipment is located and how to access it quickly.
Regular Drills and Updates
Regular drills and updates to the emergency response plan are necessary to maintain a high level of preparedness. Drills help reinforce the procedures and allow for the identification of any weaknesses in the plan.
Drills and Updates:
- Frequency: Conduct emergency drills at least twice a year, or more frequently if the site conditions or risks change. Each drill should be reviewed and evaluated for effectiveness.
- Scenario Variety: Use different scenarios for each drill to ensure that workers are prepared for various types of emergencies. This can include fire drills, medical emergency simulations, and equipment failure scenarios.
- Feedback and Improvement: After each drill, gather feedback from participants to identify any areas for improvement. Use this feedback to update the emergency response plan and address any gaps.
- Plan Review: Regularly review and update the emergency response plan to reflect changes in site conditions, personnel, or potential hazards. Ensure that any updates are communicated to all workers and incorporated into training sessions.
Emergency Equipment and Resources
Having the right emergency equipment and resources readily available is crucial for effective emergency response. This equipment must be maintained in good condition and easily accessible to workers.
Essential Emergency Equipment:
- Fire Extinguishers: Place fire extinguishers at strategic locations around the site, especially near flammable materials and equipment. Regularly inspect and maintain them to ensure they are operational.
- First Aid Kits: Stock first aid kits with essential supplies such as bandages, antiseptics, gloves, and splints. Place kits in easily accessible locations and regularly check them to replenish supplies.
- Eye Wash Stations: Install eye wash stations in areas where workers are exposed to chemicals or dust. Ensure that they are operational and accessible at all times.
- Spill Containment Kits: Provide spill containment kits for managing chemical spills. These kits should include absorbent materials, neutralizers, and personal protective equipment (PPE).
- Emergency Lighting: Ensure that emergency lighting is available and functional in case of power outages. This includes backup generators and battery-powered lights.
Summary of Emergency Preparedness
Preparedness Aspect | Description |
---|---|
Emergency Response Plan | Develop a comprehensive plan outlining procedures for various emergencies. |
Training and Familiarization | Train workers on the emergency plan, including roles, evacuation routes, and equipment use. |
Regular Drills and Updates | Conduct regular drills to practice and evaluate emergency procedures. |
Emergency Equipment and Resources | Ensure that necessary equipment is available, accessible, and maintained. |
Feedback and Improvement | Gather feedback after drills and update the plan to address any weaknesses. |
Conclusion
Excavator safety is a multi-faceted aspect of construction site management that requires diligence, proper training, regular maintenance, and robust emergency preparedness. By adhering to the guidelines and best practices outlined in this comprehensive guide, construction companies can significantly reduce the risk of accidents, protect their workforce, and enhance overall productivity.
FAQ
What are the most common causes of excavator accidents?
The most common causes include operator error, equipment failure, and poor site management.
How often should excavators be inspected?
Excavators should be inspected daily, with more thorough checks conducted monthly or quarterly.
What PPE is essential for excavator operators?
Essential PPE includes helmets, gloves, safety glasses, and high-visibility clothing.
How can communication be improved on construction sites?
Using clear signals, radios, and regular briefings can significantly improve communication.
What should be included in an emergency response plan?
An emergency response plan should include procedures for various emergencies, contact information for emergency services, and locations of emergency equipment.