Introduction
A grapple is an essential attachment for excavators that allows the machine to grasp, lift, and move materials efficiently. Grapples come in many types, sizes and configurations to match various excavator models and handle different materials. As excavation projects and equipment continue to advance, some may wonder whether the traditional excavator grapple remains necessary or if newer high-tech options are making it obsolete. This article will explore the ongoing relevance of grapples for modern excavators.
Benefits of Using A Grapple
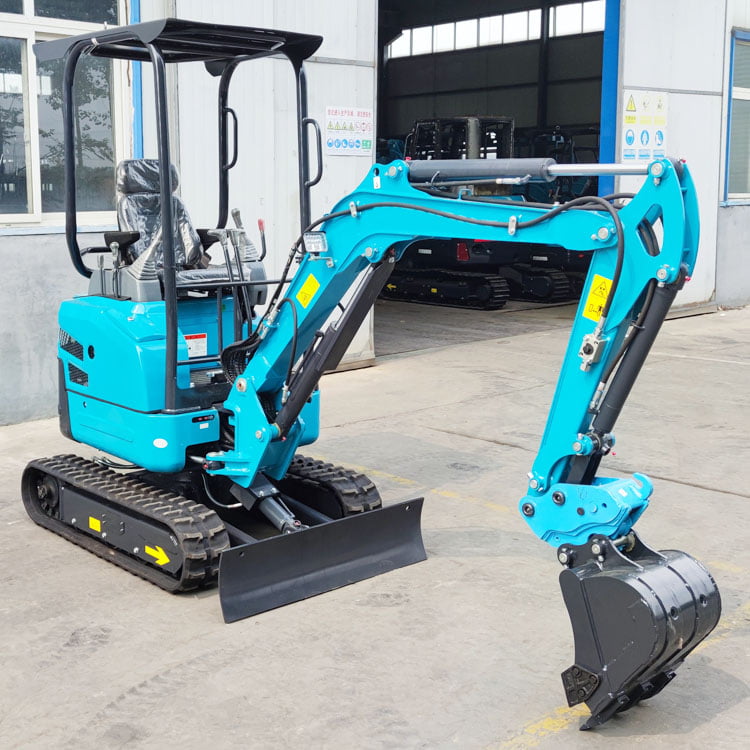
Grapples provide excavators and their operators with several key benefits that new technology has not yet replaced. Some top reasons grapples are still hugely beneficial attachments include:
- Versatility – Grapples adapt to handle many types of materials from pipes to logs to construction debris. Their ability to clamp, hold, and secure uneven loads remains unmatched.
- Safety – Grapples provide a secure way to lift materials minimizing risk of load imbalance or shifting that could tip equipment. Their durability also prevents materials from slipping loose and falling.
- Efficiency – Skilled operators use grapples to grab multiple pieces or entire piles of materials in one swoop greatly speeding up excavation and loading tasks. Precision movement also allows placing materials exactly where needed.
- Cost Savings – Grapples pair excellent functionality with reasonable costs not only for the attachment but also by enabling faster truck loading, precise object placement, and less wear on excavator buckets. Their versatility also eliminates costs of alternate specialized attachments.
While grapples may seem dated, these core benefits paired with durability and affordability make them a valuable attachment for most excavators.
Types of Excavator Grapples
While all grapples share the basic ability to grasp and move materials, they can differ greatly in design and capabilities. Common types of grapples used across industries include:
Type | Description | Typical Weights Handled |
---|---|---|
Light Material Grapple | Typically feature two thin tines perfect for precise grasping of light objects such as pipes, logs, sheets etc. | Up to 3 tons |
Scrap & Waste Grapple | Built very ruggedly with pointed tines to penetration & grab demolition debris, bins etc. | 5-15 tons |
Log Grapple | Long tines spread far apart distribute weight to safely lift & handle multiple logs at once. | Up to 10 tons |
Dense Material Grapple | Reinforced short tines allow scooping & securing heavy loose material such as gravel, scrap metal etc. | 8-30+ tons |
The optimal grapple depends primarily on the materials being handled and excavator size. Purpose built designs remain extremely effective for common excavation tasks.
Maximizing Grapple Performance
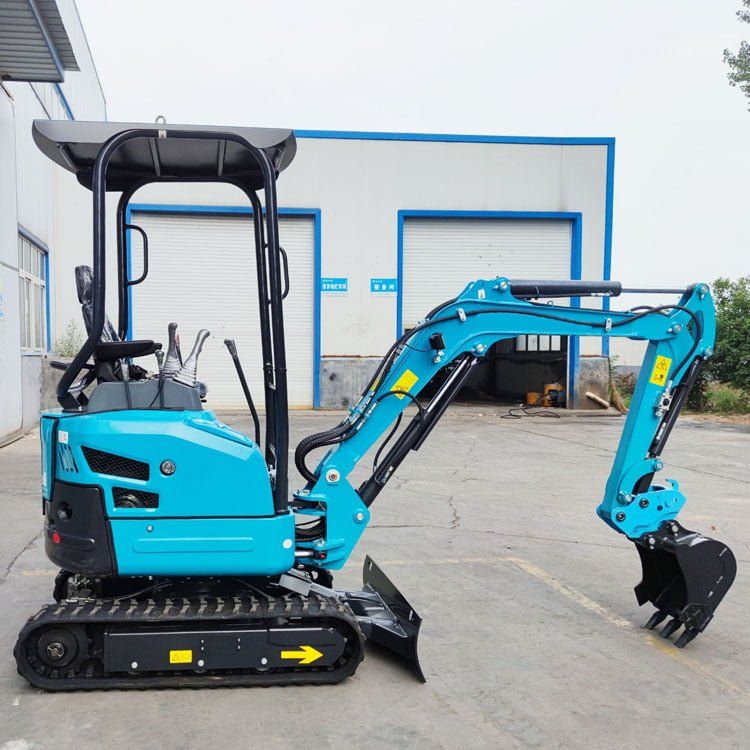
While grapples are simple in concept their efficient use requires some technique and know-how to achieve peak performance. Useful tips operators can utilize include:
- Choose the Right Grapple – Match grapple type & size to materials and excavator capability
- Adjust Tine Spread – Alter space between tines to best match & secure the load
- Use Firm, Steady Grips – Clamp materials decisively without shaking to prevent slipping
- Lift Vertically – Raise loads straight up then towards excavator to maximize stability
- Carry Loads Low – Keep lifted grapples close to the ground for best machine balance
- Use Grading Mode – Angle bucket down so grapple can support instead of lift entire load weight
- Avoid Overloading – Do not exceed grapple capacity to prevent failures or accidents
An optimal grapple attachment operated skillfully makes tough excavation jobs much simpler and efficient. The technology remains extremely relevant even as other designs advance.
Advanced and Smart Grapple Designs
While traditional grapple attachments perform excellently, some enhanced designs are beginning to appear incorporating advanced features such as:
- Quick Couplers – Allow changing grapple attachments faster with no manual installation.
- Rotators – Provide powered rotation for optimal positioning of awkward loads.
- Sensors – Motion sensors feed positioning data to help operators manipulate loads.
- Cameras – Provide visual monitoring of grappled materials via connected displays.
- Automation – Semi-autonomous grapple movement via integrated software.
- Remote Operation – Allows grapple control from a distance via networked controls.
These innovations demonstrate the potential for more technologically advanced grapples yet widespread adoption is still limited by increased costs and reliability concerns. For most common excavation tasks basic grapple attachments still prove to be the most practical and affordable choice. Grapples seem poised to continue playing a vital role in excavation work even as technology enhances other areas of these versatile machines.
Conclusion:Grapple for Excavator
Although the basic grapple attachment design has changed little over decades of use on excavators their core functionality has yet to be surpassed. Grapples match the flexibility, efficiency and affordability needed across countless excavation applications in construction, demolition, mining and more. Advanced features may emerge but the traditional grapple remains a simple, durable and effective way to extend the capabilities of any excavator. With so many models still relying daily on these attachments, grapples show no signs of becoming obsolete anytime soon! They provide capabilities nothing else matches for moving loose materials of all types. Any contractors needing to lift, grab and place all manner of objects will find grapples as relevant as ever.
FAQ
Do excavators require grapple attachments to function?
No. Excavators use a bucket as the main attachment for digging and grading work. Grapples simply extend capabilities for grasping awkward loose objects a bucket cannot easily scoop. They are very useful attachments but not mandatory for core excavating tasks.
What materials can excavator grapples handle?
Grapples handle a huge range of loose materials of various weights across industries. Typical examples include pipes, logs, demolition debris, rocks/concrete chunks, scrapped metal etc. Models with customized tines also grapple sand, mulch, trash and much more.
Will smart grapples replace traditional models?
Likely not anytime soon. Advanced grapples remain far more expensive and less proven for rugged daily use. Traditional grapples get the jobs done, especially on smaller excavators. Smart capabilities may grow in popularity but are still supplementary to core grapple functionality.
Can I use multiple grapple attachments with a single excavator?
Yes. Quick coupler hydraulic attachments make swapping various grapples on and off straightforward. A single excavator might use a light grapple for precision work but a heavy scrap grapple for demolition/junk handling using the same quick coupler mount.
What size excavator do I need for grapple use?
Mini excavators and sometimes skid steers can utilize smaller grapples but real versatility starts around 12,000lbs (5,500kg) and up. Medium to large excavators offer the hydraulic power, lift height, and space for diverse grapple applications. The optimal size depends on the loads you aim to handle.