Introduction
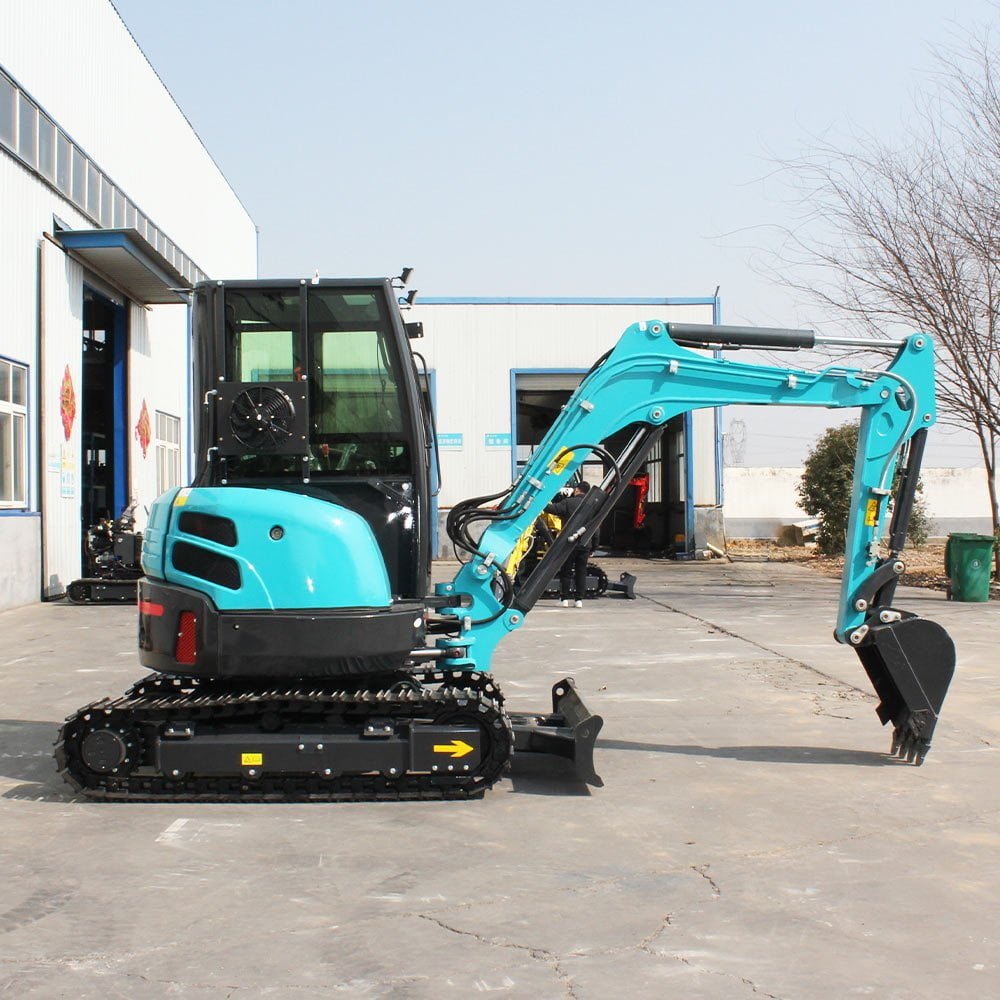
In the construction industry, the role of excavators is crucial for a variety of tasks such as digging, lifting, and moving materials. Among the various types, the Excavator 3.5 Ton stands out for its versatility and efficiency. This article aims to provide a comprehensive guide on how to maximize efficiency with an Excavator 3.5 Ton. We will cover essential aspects including operation tips, maintenance practices, common issues, and FAQs. By the end of this article, you will have a deep understanding of how to get the most out of your Excavator 3.5 Ton.
Understanding the Excavator 3.5 Ton
Specifications and Features
The Excavator 3.5 Ton is a compact and powerful machine designed to handle a variety of tasks on construction sites. Its versatility makes it an essential tool for many projects, from small residential jobs to larger commercial undertakings. Here, we delve into the specifications and features that set the Excavator 3.5 Ton apart.
Key Specifications
Operating Weight: The excavator has an operating weight of 3.5 tons, which provides a balance between mobility and stability. This weight class allows the machine to perform efficiently in confined spaces while still offering sufficient power for demanding tasks.
Engine Power: Equipped with an engine that delivers between 30 to 40 horsepower, the Excavator 3.5 Ton is capable of handling various digging and lifting operations with ease. The engine is designed for fuel efficiency and reliability, ensuring minimal downtime and operational costs.
Bucket Capacity: The standard bucket capacity ranges from 0.1 to 0.2 cubic meters, making it suitable for digging trenches, holes, and foundations. This range of capacity allows operators to choose the right bucket size for their specific needs, enhancing the machine’s versatility.
Maximum Digging Depth: With a maximum digging depth of approximately 3.0 meters, this excavator can reach deep enough for most residential and light commercial applications. This depth capability is crucial for tasks such as utility installations, landscaping, and small-scale excavation projects.
Swing Speed: The swing speed of 10 to 12 RPM allows for quick and efficient movement of the boom and bucket. This speed is essential for tasks that require frequent repositioning, such as loading trucks or moving materials around a job site.
Notable Features
Compact Design: One of the standout features of the Excavator 3.5 Ton is its compact design. This makes it ideal for operating in tight spaces where larger machines cannot fit. Urban construction sites, residential areas, and indoor projects greatly benefit from the maneuverability of this compact excavator.
Advanced Hydraulics: The hydraulic system of the Excavator 3.5 Ton is designed for smooth and precise operation. Advanced hydraulic technology ensures that the machine can perform delicate tasks with accuracy, such as grading and leveling, as well as more demanding tasks like heavy lifting and digging.
Fuel Efficiency: Fuel efficiency is a critical consideration for any construction equipment. The Excavator 3.5 Ton is engineered to minimize fuel consumption while maintaining high performance. This not only reduces operational costs but also contributes to environmental sustainability.
Operator Comfort: The operator’s comfort is paramount for maintaining productivity and reducing fatigue. The excavator’s cabin is ergonomically designed with intuitive controls, adjustable seating, and excellent visibility. Features such as climate control and noise reduction further enhance the operator’s comfort.
Ease of Maintenance: Regular maintenance is crucial for the longevity and reliability of any machinery. The Excavator 3.5 Ton is designed with ease of maintenance in mind. Accessible service points, clear maintenance schedules, and readily available parts ensure that the machine can be kept in optimal condition with minimal downtime.
Applications and Versatility
The Excavator 3.5 Ton is not just a machine; it’s a versatile tool that can be adapted for various applications. Some common uses include:
- Trenching and Excavation: Perfect for creating trenches for utilities or foundations.
- Landscaping: Ideal for grading, digging, and moving materials in landscaping projects.
- Demolition: Can handle light demolition tasks, such as breaking concrete and removing debris.
- Material Handling: Useful for loading and unloading materials, thanks to its precise control and lifting capabilities.
Operational Tips for Maximum Efficiency
Pre-Operation Checklist
Before starting the Excavator 3.5 Ton, it’s essential to conduct a thorough pre-operation check. This ensures safety and efficiency during operation. Key items to check include:
- Fluid Levels: Check hydraulic oil, engine oil, and coolant levels.
- Tire and Track Condition: Inspect for any wear or damage.
- Control Systems: Test all controls for smooth operation.
- Safety Features: Ensure all safety mechanisms are functional.
Efficient Digging Techniques
To maximize efficiency while digging with an Excavator 3.5 Ton, consider the following techniques:
- Optimal Digging Angle: Maintain a consistent digging angle to reduce stress on the machine and increase productivity.
- Bucket Positioning: Keep the bucket teeth sharp and positioned correctly to maximize digging efficiency.
- Smooth Operation: Avoid abrupt movements to prevent wear and tear on the machine.
Fuel Management
Fuel efficiency is crucial for reducing operational costs. Here are some tips to manage fuel consumption effectively:
- Idle Reduction: Turn off the engine during prolonged periods of inactivity.
- Load Management: Avoid overloading the bucket to prevent excessive fuel consumption.
- Regular Maintenance: Keep the engine and hydraulics in good condition to ensure optimal fuel efficiency.
Maintenance Practices
Regular Maintenance Schedule
Adhering to a regular maintenance schedule is key to maximizing the lifespan and efficiency of your Excavator 3.5 Ton. The following table provides a sample maintenance schedule:
Maintenance Task | Frequency |
---|---|
Engine Oil Change | Every 250 hours |
Hydraulic Fluid Check | Every 100 hours |
Air Filter Replacement | Every 500 hours |
Track Inspection | Weekly |
Cooling System Check | Monthly |
Common Maintenance Tasks
- Engine Oil and Filter Changes: Regularly changing the engine oil and filters ensures smooth engine performance.
- Hydraulic System Maintenance: Check for leaks and ensure hydraulic fluid levels are adequate.
- Track and Undercarriage Care: Regularly inspect tracks for wear and adjust tension as needed.
- Electrical System Checks: Ensure all electrical components are functioning correctly.
Troubleshooting Common Issues
Even with regular maintenance and careful operation, issues can sometimes arise with an Excavator 3.5 Ton. Identifying and addressing these problems promptly can help minimize downtime and maintain productivity. Here, we delve deeper into common issues encountered with the Excavator 3.5 Ton and provide detailed troubleshooting steps.
Engine Problems
Starting Issues
Starting issues can be frustrating and disruptive. If your Excavator 3.5 Ton is having trouble starting, consider the following troubleshooting steps:
- Battery Check: Ensure the battery is fully charged and the connections are clean and secure. Corrosion or loose connections can prevent the engine from starting.
- Fuel Supply: Verify that there is enough fuel in the tank and that the fuel supply is not obstructed. Clogged fuel filters or airlocks in the fuel line can also cause starting problems.
- Ignition System: Inspect the ignition system, including spark plugs and ignition coils. Worn or damaged components may need to be replaced to restore proper starting function.
Overheating
Overheating can lead to severe engine damage if not addressed promptly. Here are steps to troubleshoot and resolve overheating issues:
- Cooling System: Check the radiator and coolant levels. Ensure there are no leaks and that the coolant is at the recommended level. Clean the radiator to remove any dirt or debris that may be obstructing airflow.
- Thermostat: A malfunctioning thermostat can cause overheating. Test the thermostat and replace it if it is not opening and closing correctly.
- Fan Operation: Ensure the cooling fan is working properly. A faulty fan can reduce airflow through the radiator, leading to overheating.
Power Loss
Experiencing a loss of power can affect the excavator’s performance and efficiency. To address power loss:
- Fuel System: Inspect the fuel system for blockages or contamination. Replace clogged fuel filters and ensure the fuel pump is functioning correctly.
- Air Filters: Dirty or clogged air filters can restrict airflow to the engine, causing power loss. Regularly clean or replace air filters to maintain optimal engine performance.
- Exhaust System: Check the exhaust system for blockages or leaks. A blocked exhaust can cause backpressure and reduce engine power.
Hydraulic System Issues
The hydraulic system is vital for the operation of an Excavator 3.5 Ton. Common hydraulic issues and their troubleshooting steps include:
Leaks
Hydraulic leaks can lead to reduced efficiency and potential system failure. To identify and fix leaks:
- Visual Inspection: Perform a visual inspection of all hydraulic hoses, fittings, and seals. Look for signs of oil leakage and wet spots.
- Pressure Test: Conduct a hydraulic pressure test to pinpoint the exact location of the leak. Replace damaged hoses, seals, or fittings as necessary.
Slow Operation
Slow hydraulic operation can decrease productivity. To troubleshoot this issue:
- Fluid Levels: Check the hydraulic fluid levels and top up if necessary. Low fluid levels can cause slow and inefficient operation.
- Pump Function: Ensure the hydraulic pump is working correctly. A worn or damaged pump may need to be repaired or replaced.
- Filters: Inspect and replace hydraulic filters regularly. Clogged filters can restrict fluid flow and slow down the system.
Erratic Movements
Erratic hydraulic movements can be dangerous and indicate underlying issues. Address this problem by:
- Control Valves: Inspect control valves for wear or damage. Sticky or malfunctioning valves can cause erratic movements and should be repaired or replaced.
- Cylinders: Check hydraulic cylinders for signs of wear or damage. Leaking or damaged cylinders can cause inconsistent operation.
- Hydraulic Fluid: Ensure the hydraulic fluid is clean and free from contamination. Dirty fluid can cause erratic behavior and should be replaced regularly.
Electrical System Failures
Electrical issues can affect various functions of the excavator. Here’s how to troubleshoot common electrical problems:
Battery Problems
Battery issues can prevent the excavator from starting and affect its electrical systems. To troubleshoot battery problems:
- Connections: Check battery terminals for corrosion and ensure they are tightly connected. Clean and secure any loose connections.
- Charge Level: Test the battery’s charge level and recharge or replace it if necessary. A weak or dead battery can cause starting issues and other electrical problems.
Wiring Issues
Faulty wiring can disrupt the operation of the excavator’s electrical systems. To address wiring issues:
- Visual Inspection: Inspect all wiring for signs of wear, damage, or corrosion. Repair or replace damaged wiring as needed.
- Continuity Test: Use a multimeter to check for continuity in the wiring. Faulty wires can cause intermittent electrical problems and should be repaired.
Sensor Failures
Sensors play a crucial role in the excavator’s operation. Faulty sensors can lead to various issues. To troubleshoot sensor failures:
- Diagnostics: Use the excavator’s diagnostic system to identify faulty sensors. Modern excavators are equipped with onboard diagnostics to pinpoint sensor issues.
- Replacement: Replace any malfunctioning sensors. Ensure that new sensors are properly calibrated and functioning correctly.
Proactive Measures
In addition to troubleshooting, taking proactive measures can prevent many common issues. Regular inspections, routine maintenance, and operator training are key to keeping your Excavator 3.5 Ton in optimal condition. Establish a maintenance schedule that includes checks for fluid levels, filters, hoses, and electrical components. Educate operators on best practices for using the excavator and recognizing early signs of problems.
Best Practices for Operator Safety
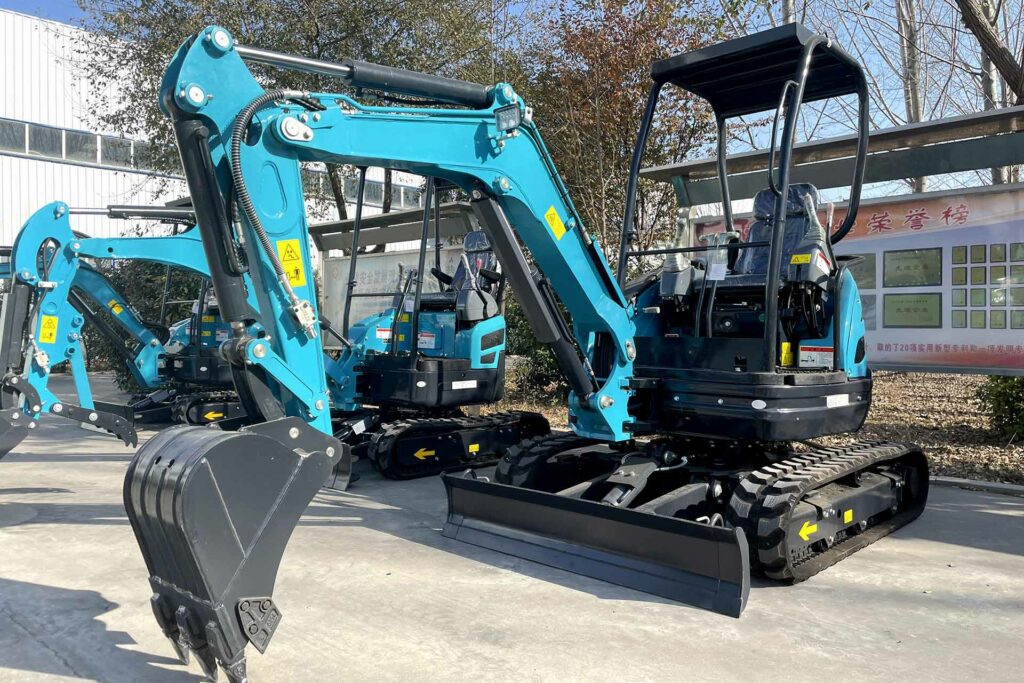
Ensuring operator safety is paramount when working with heavy machinery such as the Excavator 3.5 Ton. Adhering to safety best practices not only protects the operator but also enhances overall site safety and productivity. Below, we provide an in-depth look at essential safety measures, training, and procedures to follow.
Training and Certification
Comprehensive Training Programs
Before operating an Excavator 3.5 Ton, operators must undergo comprehensive training. This training should cover:
- Machine Operation: Detailed instructions on how to operate the excavator, including starting, maneuvering, and using various attachments.
- Safety Protocols: Training on safety protocols specific to the excavator, such as emergency shut-down procedures and the use of safety features.
- Maintenance Practices: Basic maintenance tasks that operators can perform to ensure the machine remains in good working condition.
Certification Requirements
Many regions require operators to be certified to operate heavy machinery. Certification ensures that operators have demonstrated their competence and understanding of safe operating procedures. Certification programs typically include:
- Written Exams: Assessing knowledge of safety rules, machine components, and operational techniques.
- Practical Tests: Evaluating the operator’s ability to safely and effectively operate the excavator in a controlled environment.
Personal Protective Equipment (PPE)
Essential PPE for Excavator Operators
Wearing the appropriate personal protective equipment (PPE) is crucial for operator safety. Key PPE items include:
- Hard Hats: Protect the head from falling objects and debris.
- Safety Glasses: Shield the eyes from dust, dirt, and flying particles.
- High-Visibility Clothing: Ensure the operator is easily seen by other workers and machinery operators on the site.
- Safety Boots: Provide foot protection against heavy objects and uneven surfaces.
- Hearing Protection: Protect the operator’s hearing in noisy environments, especially if the excavator is operating for extended periods.
Safe Operating Procedures
Pre-Operation Inspection
Conducting a pre-operation inspection is essential to identify any potential issues before starting the machine. This includes:
- Visual Checks: Inspect the excavator for any visible signs of damage or wear, such as cracks, leaks, or loose components.
- Fluid Levels: Check engine oil, hydraulic fluid, coolant, and fuel levels.
- Controls and Gauges: Ensure all controls and gauges are functioning correctly.
Safe Start-Up and Shut-Down
Proper start-up and shut-down procedures help prevent accidents and mechanical issues:
- Start-Up: Follow the manufacturer’s start-up procedure, which typically includes checking the surroundings, ensuring the machine is in neutral, and engaging the parking brake.
- Shut-Down: Lower the boom and bucket to the ground, engage the parking brake, and turn off the engine. Conduct a post-operation inspection to identify any new issues.
Safe Operation Techniques
Implementing safe operation techniques can significantly reduce the risk of accidents:
- Clear Communication: Use hand signals or radios to communicate with ground personnel. Establish a clear communication protocol to avoid misunderstandings.
- Awareness of Surroundings: Always be aware of the excavator’s surroundings, including other workers, machinery, and potential hazards. Regularly check mirrors and cameras (if equipped) to maintain situational awareness.
- Load Limits: Adhere to the manufacturer’s recommended load limits. Overloading the excavator can lead to tipping or mechanical failure.
- Stable Positioning: Ensure the excavator is on stable, level ground before performing any digging or lifting operations. Use stabilizers if necessary.
Emergency Preparedness
Emergency Procedures
Operators should be trained in emergency procedures to respond effectively to unexpected situations:
- Emergency Shut-Down: Know how to quickly and safely shut down the excavator in case of an emergency, such as a hydraulic failure or fire.
- First Aid: Basic first aid training can help operators provide immediate assistance in case of an injury until professional medical help arrives.
- Evacuation Plans: Be familiar with the site’s emergency evacuation plan and the locations of emergency exits and assembly points.
Regular Drills
Conduct regular safety drills to ensure that all operators and site personnel are familiar with emergency procedures. Drills should simulate various scenarios, such as fire, equipment failure, or medical emergencies.
Continuous Improvement
Safety Audits
Regular safety audits can help identify potential risks and areas for improvement:
- Internal Audits: Conduct internal audits to review safety procedures and compliance with safety standards.
- External Audits: Engage third-party safety experts to perform external audits and provide unbiased assessments and recommendations.
Feedback and Reporting
Encourage operators to provide feedback on safety practices and report any incidents or near-misses:
- Incident Reporting: Establish a clear process for reporting incidents and near-misses. Analyze reports to identify trends and develop preventive measures.
- Operator Feedback: Regularly gather feedback from operators regarding safety practices and equipment performance. Use this feedback to make informed decisions about training, equipment upgrades, and procedural changes.
Conclusion
Maximizing efficiency with an Excavator 3.5 Ton involves a combination of proper operation, regular maintenance, and adherence to safety practices. By following the tips and guidelines provided in this article, you can ensure that your Excavator 3.5 Ton operates at peak performance, reducing downtime and operational costs. Whether you are a seasoned operator or new to using an excavator, these best practices will help you get the most out of your machine.
FAQ
What is the maximum digging depth of the Excavator 3.5 Ton?
The Excavator 3.5 Ton has a maximum digging depth of approximately 3.0 meters.
How often should the engine oil be changed?
The engine oil should be changed every 250 hours of operation.
What type of fuel is recommended for the Excavator 3.5 Ton?
Diesel fuel is recommended for the Excavator 3.5 Ton.
How can I improve the fuel efficiency of my excavator?
To improve fuel efficiency, reduce idling time, avoid overloading, and ensure regular maintenance of the engine and hydraulics.
What are the common signs of hydraulic system problems?
Common signs include slow operation, erratic movements, and visible leaks in the hydraulic system.