Introduction
A 5 ton excavator, sometimes called a mini excavator, is a popular piece of construction equipment used for digging, lifting, and moving materials. 5 ton refers to the operating weight of the excavator, with typical units in this class weighing between 4.5 and 6 tons. These compact excavators provide excellent maneuverability and versatility on construction sites.
However, 5 ton excavators also come with safety risks and hazards that operators should be aware of. In this blog post, we will highlight the 5 top risks associated with 5 ton excavators and steps that can be taken to minimize danger. Having a clear understanding of the major risks can help improve operator safety and reduce accidents on the jobsite.
Rollovers
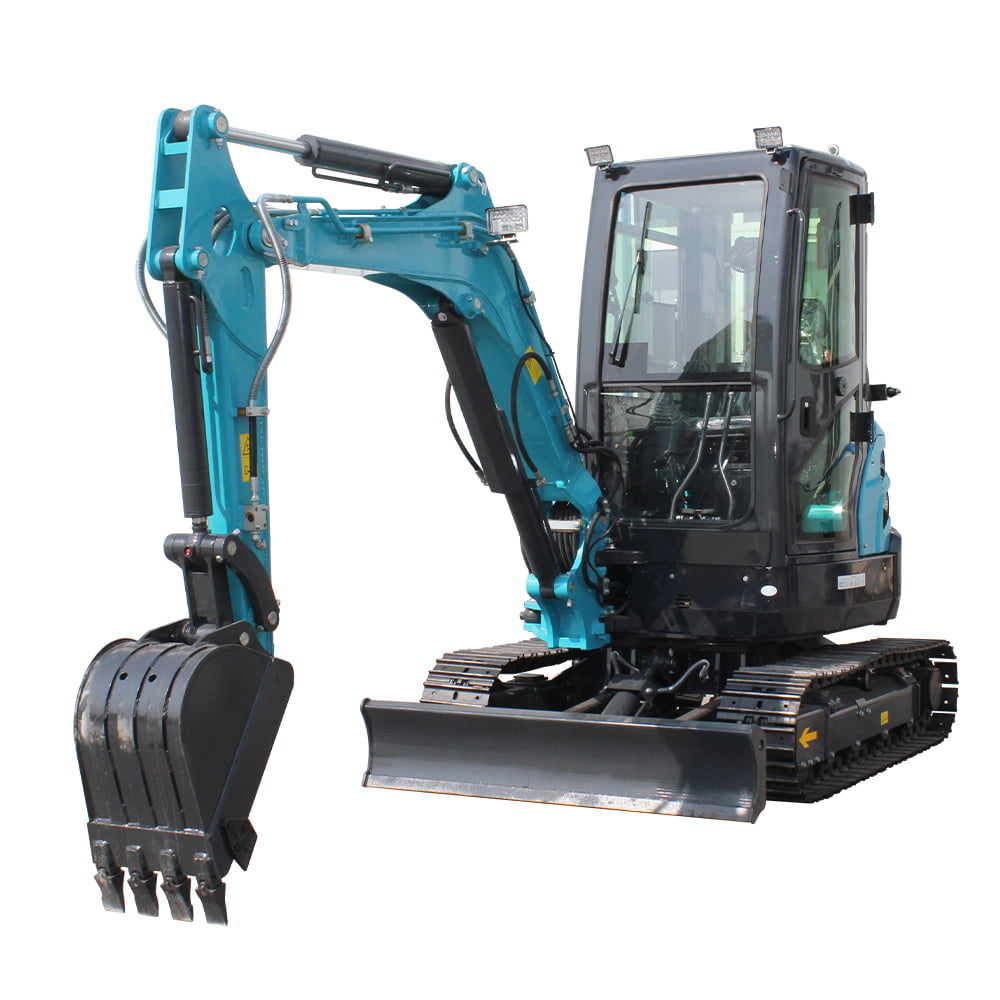
Rollovers represent one of the greatest and most serious risks when operating 5 ton excavators. Statistics show that excavator rollovers make up around 20-30% of all recorded excavator accidents.
Some key reasons why rollovers occur include:
- Working on uneven/unstable ground
- Working on inclines or slopes
- Sudden movements when swinging the boom
- Overloading the bucket or attachments
- Poor visibility around the equipment
To prevent rollovers, operators should:
- Check ground conditions before starting work
- Avoid inclines and slopes greater than 20 degrees
- Operate smoothly without sudden load shifts
- Follow load limits for buckets and attachments
- Ask for help directing when visibility is low
Objects Falling from Buckets
5 ton excavators are commonly used for demolition work, which involves breaking structures and handling debris. A major risk is objects falling uncontrolled from the excavator bucket onto workers below.
Falling objects can cause injuries from impact or crushing, namely:
- Head and body trauma
- Broken bones
- Bruises and cuts
To help avoid falling objects:
- Clear debris rather than letting objects pile up
- Carry loads close to the ground when moving
- Tilt bucket downward when lifting high
- Keep workers and equipment out from under loads
- Use nets/sheets to contain small objects
Power Line Contact
Coming into contact with overhead power lines presents an electrocution hazard to excavator operators. This poses greater risks on urban construction sites where buildings and supply infrastructure encroach close to the work area.
- Cranes and excavators account for around 70% of power line-related accidents each year
- Contact can occur even when not directly touching lines (electricity can arc/jump)
- Power line contact can result in electrocution, burns, falls, or equipment damage
Preventing power line accidents involves:
- Identifying all supply lines before starting work
- Planning safe equipment operating zones away from power lines
- Appointing spotters when working near overhead lines
- Using insulating protection on equipment as practical
Table 1 summarizes recommendations for minimum safe working distances from different voltage power lines.
Line Voltage | Minimum Safe Clearance Distance |
---|---|
0 – 50 kV | 3 meters |
50 – 200 kV | 5 meters |
200 – 350 kV | 6 meters |
350 – 500 kV | 8 meters |
500 – 750 kV | 11 meters |
Above 750 kV | 13 meters |
Musculoskeletal Injuries
5 ton excavators require repetitive motion and handling of heavy controls, which can lead to back strain, joint pain, tendonitis, carpal tunnel syndrome, and other musculoskeletal disorders over time.
- Bad postures like twisting, bending, reaching contribute
- Exposure to whole body vibration transfers to body
- Cold weather can exacerbate conditions
Steps to minimize physical overexertion include:
- Adjusting seat and controls to natural positions
- Keeping joints in neutral positions as possible
- Using smooth, steady movements without jerking
- Taking breaks to stretch and change positions
- Wearing vibration-dampening gloves and clothes
MSD risks can be assessed using a simple 1-10 scale for different body parts:
Body Area | Risk Rating | Action |
---|---|---|
Back | 7 | Seek ergonomic assessment |
Shoulders | 3 | Monitor for further symptoms |
Hands/wrists | 5 | Evaluate alternate control configurations |
Slips and Falls
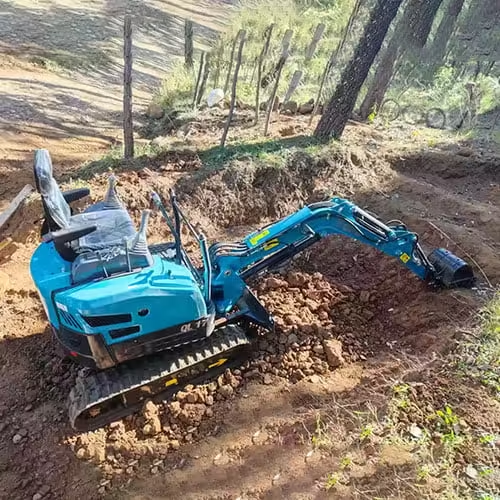
Though excavators have reinforced cabs, operators still face slips and falls getting in and out of the equipment. Descending from several feet height means falls can cause serious bodily harm.
Hazards stem from:
- Insufficient or missing steps and handholds
- Wet, muddy, slippery conditions
- Debris left around access areas
- Poor visibility when exiting cab
Fall protection should focus on:
- Installing secure steps, rails, and non-slip surfaces
- Maintaining 3-point contact when mounting/dismounting
- Sitting down facing outwards before getting out
- Keeping vision clear and carrying only what can be handled safely
Conclusion:5 Ton Excavator
In summary, 5 ton excavators deliver versatility and performance important for construction sites, but also carry safety risks like rollovers, falling objects, power lines, MSDs, and falls that require dedicated prevention efforts. Companies must establish thorough training, protocols, and hazard awareness to keep operators of 5 ton excavators protected on the job. Managing these top 5 risks ultimately depends on coordination between workers, supervisors, and safety managers.
FAQ
Q: What are the most common excavator-related injuries?
A: Statistics show the most common injuries are struck-bys when objects fall from buckets, and musculoskeletal disorders from repetitive motion and vibration. Overturns and electrocutions are rarer but lead to more serious harm.
Q: Should a spotter always be used near power lines?
A: Yes, designated spotters should be assigned to observe minimum clearance distances and warn operators whenever work encroaches near live power lines. Trying to do both tasks at once leads to excessive distraction and accidents.
Q: How can companies improve mini excavator safety?
A: Key elements include developing comprehensive safety plans, ensuring regular maintenance, establishing site hazard controls, mandating certified operator training, promoting strong safety culture, and investing in modern safe-design excavators equipped with features like rollover protection, fall restraints, and camera systems.
Q: What are some advanced safety technologies for excavators?
A: Modern innovations to improve excavator safety include proximity sensors and alerts to prevent collisions, load moment indicators to reduce overloading risks, anti-slip cab floors, finger guards for hand controls, fatigue/distraction monitoring cameras, and satellite links for remote equipment tracking and geofencing.